DOI:
10.1039/D0RA10102H
(Paper)
RSC Adv., 2021,
11, 4942-4951
N/Fe/Zn co-doped TiO2 loaded on basalt fiber with enhanced photocatalytic activity for organic pollutant degradation
Received
30th November 2020
, Accepted 12th January 2021
First published on 26th January 2021
Abstract
To avoid the loss of catalytic material powder, a loaded catalytic material of TiO2 with basalt fiber as the carrier (TiO2@BF) was synthesized by an improved sol–gel method. The TiO2@BF was doped with different contents of N, Fe and Zn elements and was used to degrade rhodamine B (RhB) under ultraviolet light. The physical characterization analysis indicated that the co-doping of the N, Fe and Zn elements had the effects of reducing grain size, increasing sample surface area, and narrowing the electronic band gap. The electronic band gap of nitrogen–iron–zinc co-doped TiO2@BF (N/Fe/Zn_TiO2@BF) was 2.80 eV, which was narrower than that of TiO2@BF (3.11 eV). The degradation efficiency of RhB with N/Fe/Zn_TiO2@BF as a photocatalyst was 4.3 times that of TiO2@BF and its photocatalytic reaction was a first-order kinetic reaction. Quenching experiments suggested that the reactive species mainly include photoinduced holes (h+), superoxide radicals (˙O2−) and hydroxyl radicals (˙OH). In brief, this study provides a prospective loaded catalytic material and routine for the degradation of organic contaminants in water by a photocatalytic process.
1 Introduction
At present, water pollution caused by man-made organic pollutants has become one of the key concerns all over the world.1–4 Large quantities of organic compounds, such as synthetic dyes and endocrine disruptors, originating from industries including textiles, plastics, pharmaceuticals, etc.,5,6 would have harmful effects on mankind and animal life in short or long periods of time. Water pollution caused by dye wastewater discharged from traditional industries, one of the most common contaminants, has attracted extensive attention.7 Rhodamine B (RhB), a typical pollutant of dye molecules,8 is difficult to be removed by self-purification of natural water systems because of its high stability and it greatly threatens human health due to its toxicity. Therefore, research into removing dye molecules in water has become a hot topic in recent years.
Nowadays, common water treatment methods mainly include membrane filtration,9 coagulation sedimentation,10 electrochemical,11 advanced oxidation process,12,13 and biological treatment14 methods. Photocatalytic oxidation, an advanced oxidation process, could efficiently eliminate various harmful organic compounds. It has attracted extensive attention in the field of water environmental protection and restoration due to the advantages of low cost, easy operation, high efficiency, low consumption, no secondary pollution, and great damage to dye molecules.
In the study of photocatalytic oxidation to degrade pollutants, TiO2 nanoparticles15 are one of the most widely studied semiconductor photocatalysts in photocatalysis due to their strong oxidizing ability, chemical stability, safety, non-toxicity, and high photocatalytic potential.16,17 However, TiO2 has some intrinsic drawbacks in practical applications such as its wide band gap and charge carrier recombination, which result in low light utilization efficiency and photocatalytic activity in the visible region.18,19 Consequently, tremendous efforts have been devoted to improving the photocatalytic efficiency of TiO2 via modification, including doping modification,20 surface modification,21 dye sensitization,22 deposition of noble metals,23,24 semiconductor recombination,25 etc. In particular, metal doping26 and non-metal doping27 for TiO2 have proved to be the most effective methods and have been extensively studied.
In addition, TiO2 nanoparticles are difficult to recycle and reuse in applications because of their small particles. In order to solve the problem of catalyst recycling and reuse, many researchers have used different substances as carriers to support TiO2 to synthesize TiO2 loaded composites, such as activated carbon, glass fiber and carbon fiber.28–30 Basalt fiber (BF) is made of pure natural basalt ore as the raw material and its main component is SiO2, which has a similar structure to TiO2. Therefore, BF, which has similar mineral properties to TiO2, could adhere to TiO2 firmly. Generally, to synthesize TiO2 loaded composites, TiO2 nanoparticles need to be prepared first and then dispersed in a sol to carry out loading. The high temperature resistance and excellent physicochemical stability of BF allows it to be loaded in the intermediate step of TiO2 preparation and then calcined to obtain the composite material in one step, thereby increasing the loading efficiency of TiO2 and saving time and cost. To the best of our knowledge, no studies on TiO2 loaded on BF for the degradation of organic contaminants in water have been reported.
In the current study, a new three-dimensional structure model was made from BF and TiO2 with three doping elements of N, Fe, and Zn loaded on the BF to prepare a multi-element co-doped TiO2@BF composite material, which has a larger contact area with water and a higher light transmittance. The synthesized new multi-element doped G_TiO2@BF (in G_TiO2@BF, G represents the dopants N, Fe and Zn) composite material was characterized. Meanwhile, the doping substance combination and the effects of the dopant content (%) of different dopants were investigated, the photocatalytic performance of the synthesized material was tested for the degradation of RhB and the possible degradation mechanisms were studied.
2 Experimental materials and methods
2.1 Chemical reagents
Tetrabutyl titanate (≥98.5%), ethyl alcohol (≥99.5%, anhydrous), and nitric acid (65–68%) were used for TiO2 synthesis. Urea (≥99.0%), ZnO (≥98.0%), and ferric nitrate nonahydrate (≥98.5%) were used as reagents when doping and modifying TiO2. Rhodamine B (RhB) was used in the photocatalytic degradation experiment. 1,4-Benzoquinone (BQ, ≥98.5%), tert-butyl alcohol (TBA, ≥99.0%) and EDTA-2Na (≥99.0%) were used in the reactive species quenching experiments. All the reagents were from Chron Chemicals Co., Ltd. (Sichuan, China). Distilled water (resistance > 18.25 MΩ), used in all experiments, was provided by a water purification system (ULUPURE, China).
2.2 Synthesis of the catalytic loaded composites
2.2.1 Colloidal sol. Typically, 200 mL of tetrabutyl titanate was added dropwise to a 1000 mL sized beaker containing 600 mL ethyl alcohol with constant mechanical stirring. After mixing, 30 mL of nitric acid was added to the mixture slowly and uniformly, then the beaker was sealed and stirring continued for 1 hour. Finally, a yellow transparent sol was obtained.
2.2.2 Doping. N_TiO2 sol, Fe_TiO2 sol and Zn_TiO2 sol were synthesized, respectively, doping substances of urea, ferric nitrate nonahydrate and ZnO with different doping ratios. The corresponding proportions were n(N)
:
n(Ti) = (6%, 8%, and 12%), n(Fe)
:
n(Ti) = (0.03%, 0.3%, and 1%), and n(Zn)
:
n(Ti) = (0.5%, 2%, and 7%). The doping substances with different doping ratios were separately dissolved in 600 mL ethyl alcohol and then the mixed solution was used as an organic solvent. The remaining steps were consistent with the preparation of the sol. After the photocatalytic degradation of RhB with single doping of TiO2@BF, the optimal doping ratio was selected to be 8% N, 0.3% Fe and 2% Zn, and then the three materials were co-doped with an optimal doping ratio of N, Fe, and Zn to obtain the N/Fe/Zn_TiO2 sol.
2.2.3 Catalytic loaded composites. After the sol was prepared, the three-dimensional model of BF shown in Fig. 1 was evenly loaded with a layer of sol by the dipping method and the second impregnation was carried out after the first layer was naturally air-dried. After that, the BF model was placed in a drying oven at a temperature of 85 °C for 50 minutes to volatilize the ethyl alcohol, then put in a muffle furnace at 400 °C and calcined for 3 hours. Finally, TiO2@BF, N_TiO2@BF, Fe_TiO2@BF, Zn_TiO2@BF and N/Fe/Zn_TiO2@BF were obtained. The TiO2 loading quantity was calculated by the mass difference between the three-dimensional model of BF without loading TiO2 and TiO2@BF.
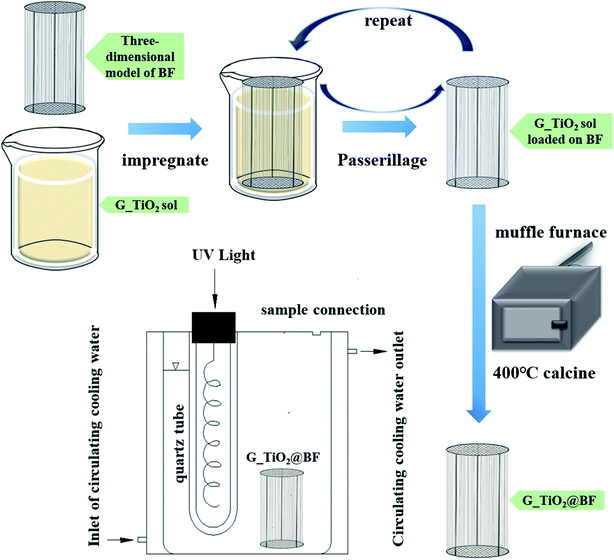 |
| Fig. 1 Preparation steps of G_TiO2@BF and the photocatalytic degradation reaction device. | |
Fig. 1 presents the preparation steps of loading TiO2 on BF and the photocatalytic degradation reaction device. The BF model was based on a round wire mesh as a fiber guide bracket; three equal-height wires were used as a wire mesh fixed bracket and 126 basalt fiber bundles were fixed at 5 mm intervals on it. Every basalt fiber bundle was 27 cm in length and 0.5 mm in diameter.
2.3 Characterization
The surface morphology and fracture morphology of the sample were examined by scanning electron microscopy (SEM, S-450, Japan). Energy dispersive spectrometry (EDS, Aztec X-Max80, UK) was applied to the qualitative analysis of elements. The crystalline phases and grain size of the samples were characterized by X-ray diffraction (XRD, EMPYREAN, UK), using Cu Kα radiation (λ1 = 1.5406 Å, λ2 = 1.5444 Å), a monochromatic slit of 0.76 mm, a 2θ diffraction angle of 10° to 80° and a scan step of 0.03° s−1. The functional groups were analyzed by Fourier transform infrared spectroscopy (FT-IR, Nicolet 6700, USA). The molecular structural groups were analyzed by Raman spectra (RAMAN, LabRAM HR800, France). The surface composition and chemical state of the sample were investigated by the AXIS Supra multifunctional X-ray photoelectron spectrometer (XPS, KRATOS, UK), using a monochromatic X-ray source. The electronic band gaps of the synthesized photocatalysts were analyzed by UV-visible diffuse-reflectance spectroscopy (UV-vis/DRS, UV-3600, Japan). The samples used for characterization like TiO2 refer to powders scratched off from the fiber and those like TiO2@BF refer to layers loaded on basalt fibers.
2.4 Photocatalytic degradation of RhB
The photocatalytic degradation of RhB was investigated under ultraviolet (UV) light in a photocatalytic dark box reactor. The experiments were performed in a 10 L cylindrical black box with a mercury lamp (42 W, λ = 235.7 nm) as the light source, and circulating water was adopted to control the reaction temperature at ambient temperature. In order to eliminate the disturbance of the adsorption, it is necessary to reach an adsorption/desorption equilibrium before turning on the light.31 After the samples of G_TiO2@BF (G represents the dopant) were added into 7 L RhB solution (5 mg L−1) for 30 min in the dark, the experiment was kept for 180 min under UV light. During the experiment, 50 mL of RhB solution was sampled at certain intervals and the supernatant solution was obtained at high-speed centrifugation before detecting the RhB concentration by spectrophotometry (V729, YOKE INSTRUMENT, China) at 554 nm. The degree of RhB degradation was expressed as Ct/C0, where Ct was the RhB concentration at the sampling time, and C0 was RhB concentration at the initial time. The stability and reusability experiment materials were washed with absolute ethanol and deionized water several times. The samples were calcined at 400 °C for 1 h before the next cycle experiment was carried out.
3 Results and discussion
3.1 Physicochemical properties
3.1.1 Crystal structure, crystallite size and morphology. The photocatalytic activity is greatly influenced by the crystal phase of TiO2. As reported, the photocatalytic activity of anatase phase TiO2 synthesized at 400 °C is better than that of the rutile phase and brookite phase.32,33 Therefore, 400 °C was selected as the calcination temperature to prepare the catalyst.Fig. 2(a) and (b) depict the microstructure and morphology of BF and TiO2@BF by SEM, from which it could be obviously observed that the fibers were wrapped with TiO2. There were many micropores on the surface of the synthesized N/Fe/Zn_TiO2@BF catalyst due to using urea as the N doping source. During the calcination process, urea could change to gas and escape, increasing the specific surface area of material. As shown in Fig. 2(c)–(h), it was confirmed that the O, Ti, N, Fe and Zn elements coexisted on the N/Fe/Zn_TiO2@BF.
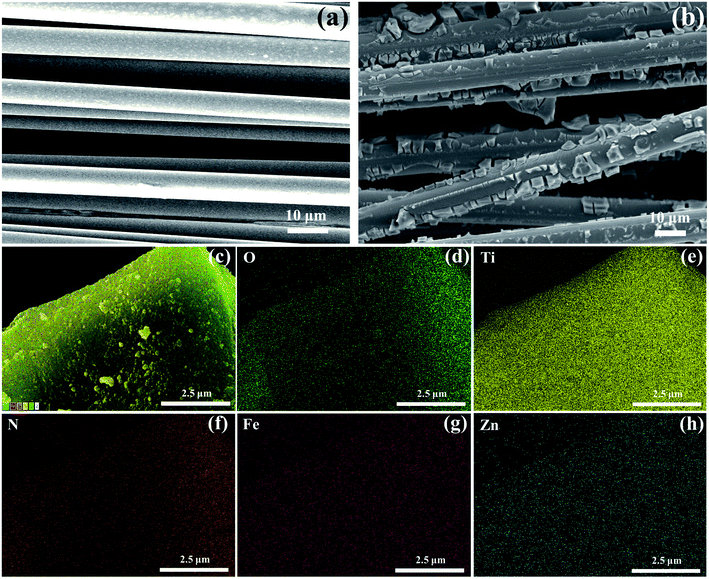 |
| Fig. 2 SEM micrographs for the samples: (a) BF and (b) TiO2@BF; EDS elemental mapping images of (c)–(h) N/Fe/Zn_TiO2@BF. | |
XRD is performed to characterize the crystal structure of the material. TiO2 was stripped from the BF surface to analyze its crystal phase due to the diffraction peak of BF covering that of TiO2. Fig. 3 depicts the XRD results of the synthesized TiO2 and N/Fe/Zn_TiO2 and TiO2@BF. The diffraction peak of synthesized TiO2 appeared at 2θ = 25.22° (101), 37.89° (004), 48.07° (200), 53.81° (105), 55.08° (211) and 62.63° (204), which matched well with the JCPDS NO: 21-1272. The result shows that the synthesized TiO2 was monocrystalline and in the pure anatase phase, which was confirmed by there being no diffraction peaks at 2θ = 27.5° (110) and 30.8° (121), corresponding to the rutile and brookite phase. The diffraction peak location of N/Fe/Zn_TiO2 also corresponded to the anatase phase, indicating that the doping of N, Fe and Zn did not change the crystal structure of pristine TiO2. In addition, the XRD spectra of N/Fe/Zn_TiO2 (Fig. 3) show no peaks of Zn oxide and Fe oxide.
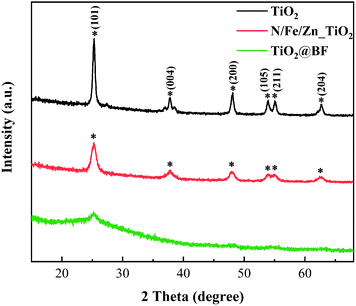 |
| Fig. 3 XRD spectra of TiO2, N/Fe/Zn_TiO2 and TiO2@BF prepared at 400 °C. | |
The crystallite sizes were calculated from the stretching of the anatase (101) peaks by using the Scherrer formula as follows.
|
D = kλ/β cos θ
| (1) |
where
D is the crystallite size (nm),
k is the Scherrer constant (0.89),
λ is the wavelength of X-ray (1.5406 Å),
β is the half-height width of the diffraction peak of the measured sample (rad), and
θ is the Bragg diffraction angle (°). The crystallite size of synthesized TiO
2 and N/Fe/Zn_TiO
2 was calculated to be 18.1 nm and 10.4 nm, respectively, which indicated that the doping of N/Fe/Zn affects the crystallite size. With the smaller particles and bigger specific surface area, the catalysts would provide more catalytic activity points, and catalytic efficiency was improved. The result that N/Fe/Zn_TiO
2 had a wider diffraction peak and a smaller relative peak strength than TiO
2 (
Fig. 3) also proves that the dopant would inhibit crystal growth. A similar result was also obtained by Ebrahim Rezaei.
29
As shown in Fig. 4(a), it was difficult to observe the vibration modes of TiO2 and N/Fe/Zn_TiO2 due to the diffraction peak of BF covering that of TiO2 in the RAMAN spectra of the synthesized TiO2@BF and N/Fe/Zn_TiO2@BF. As displayed in Fig. 4(b), their TiO2 crystals were both in the anatase phases. As could be seen from Fig. 4(b), the positions of the characteristic bands in the synthesized TiO2 of 143.2, 197, 395.4, 515 and 639 cm−1 correspond to the vibration modes of Eg, Eg, B1g, A1g and Eg in the single crystal anatase phase, respectively. The result that only five vibration modes appeared was lower than the six Raman activation modes (A1g + 2B1g + 3Eg) reported by Ohsaka34 because the peaks at positions 513 and 515 cm−1 overlap; a similar result was also obtained by Choi35 and Cho.36 In Fig. 4(b), no characteristic bands were observed at 445 and 612 cm−1, indicating that the rutile phase did not exist in the prepared TiO2 sample. Compared with the characteristic peaks of TiO2, the characteristic peaks of N/Fe/Zn_TiO2 were weakened and the half-peak width increased due to the decrease of crystallinity size after doping, which was consistent with the XRD results.
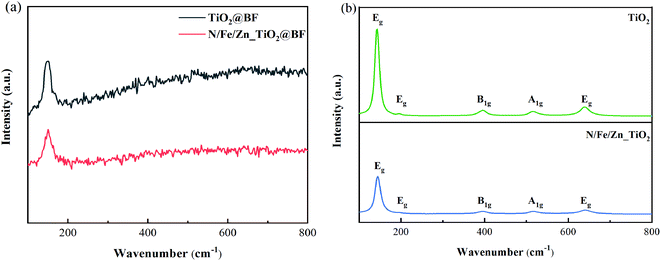 |
| Fig. 4 RAMAN spectra of (a) TiO2@BF and N/Fe/Zn_TiO2@BF and (b) TiO2 and N/Fe/Zn_TiO2 prepared at 400 °C. | |
3.1.2 Chemical state, electronic structure and electronic band gaps. The chemical composition of the surface of TiO2@BF and N/Fe/Zn_TiO2@BF was determined by XPS, as shown in Fig. 5. Compared with the full XPS spectrum of TiO2@BF (Fig. 5(a)), the characteristic peaks of Zn and N appeared in the full XPS spectrum of N/Fe/Zn_TiO2@BF (Fig. 5(b)) but the Fe signal was not detected due to the low content of Fe in N/Fe/Zn_TiO2@BF. The Zn 2p core spectrum in Fig. 5(c) shows that the peaks of 1045.08 eV and 1021.97 eV correspond to Zn 2p1/2 and Zn 2p2/3, respectively, indicating that Zn in N/Fe/Zn_TiO2@BF had a +2 valence.37 Meanwhile, all Zn exist in the Zn2+ state and Zn 2p3/2 bonds or coordinates with oxygen.38 Fig. 5(d) shows a peak at 401.22 eV of the N 1s core spectrum of N/Fe/Zn_TiO2@BF from the Gaussian fitting curve, indicating that N was oxidized to form a Ti–O–N bond.39 In Fig. 5(e), it could be seen that the binding energy values were 464.22 eV and 458.48 eV, belonging to Ti 2p1/2 and Ti 2p3/2, respectively, indicating the appearance of Ti4+.40,41 As shown in Fig. 5(f), the co-doping of N, Fe and Zn did not change the valence state of Ti, which was still in the valence state of Ti4+. As observed in Fig. 5(g), the O 1s spectra of TiO2 could be divided into two peaks at 529.76 eV and 539.72 eV, corresponding to Ti–O–Ti and surface defects or surface hydroxy-groups, respectively.42 In Fig. 5(h), the co-doping did not change the state of O 1s.
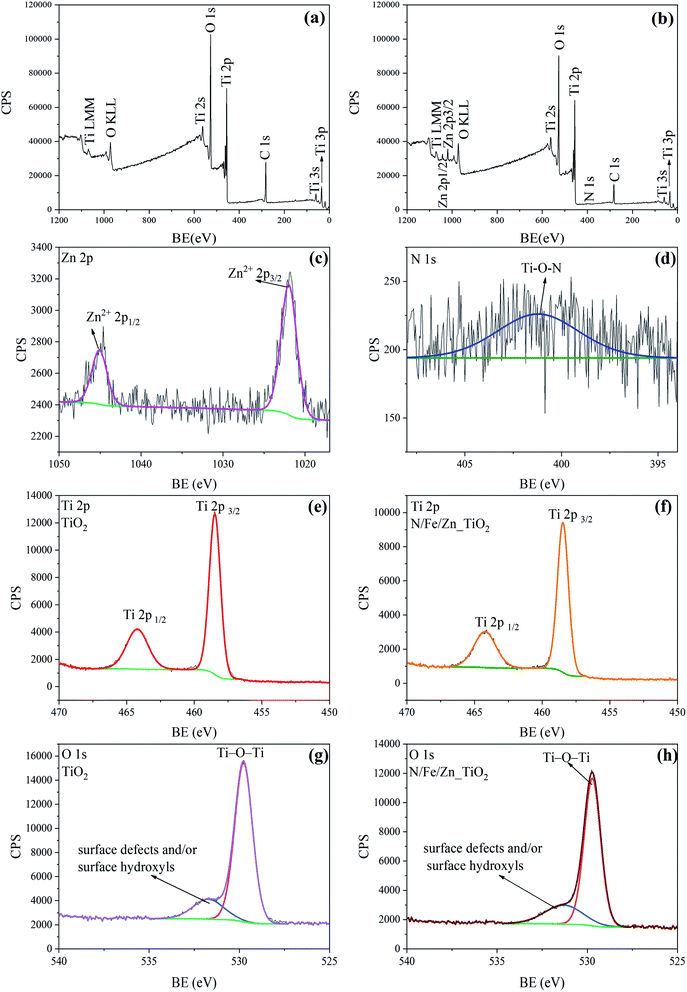 |
| Fig. 5 XPS surface analysis for TiO2@BF and N/Fe/Zn_TiO2@BF: (a) TiO2@BF full XPS spectrum, (b) N/Fe/Zn_TiO2@BF full XPS spectrum, (c) Zn 2p core level spectra of N/Fe/Zn_TiO2@BF, (d) N 1s core level spectra of N/Fe/Zn_TiO2@BF, (e) Ti 2p core level spectra of TiO2@BF, (f) Ti 2p core level spectra of N/Fe/Zn_TiO2@BF, (g) O 1s core level spectra of TiO2@BF, and (h) O 1s core level spectra of N/Fe/Zn_TiO2@BF. | |
The real doping contents for N/Fe/Zn_TiO2@BF were calculated from the quantitative method of the XPS sensitivity factor by using the following formula.
|
Cx = (Ax/Sx)/(ΣAi/Si)
| (2) |
where
Cx is the concentration of the element at the surface,
Ax is the XPS peak area of the desired element,
Sx is the relative sensitivity factor of the XPS peak (the RSF of N 1s, Zn 2p and Ti 2p is 0.477, 5.589 and 2.001, respectively), Σ
Ai/
Si is the sum of the ratio of the peak area to the relative sensitivity factor of all the measured elements. The XPS peak area values of N 1s, Zn 2p and Ti 2p were 141.55, 2466.49 and 26
![[thin space (1/6-em)]](https://www.rsc.org/images/entities/char_2009.gif)
432.85, obtained from the XPS spectrum of N/Fe/Zn_TiO
2@BF. When the concentration ratio was obtained, the molar ratio could be further calculated to be
n(N)
![[thin space (1/6-em)]](https://www.rsc.org/images/entities/char_2009.gif)
:
n(Ti) = 8% and
n(Zn)
![[thin space (1/6-em)]](https://www.rsc.org/images/entities/char_2009.gif)
:
n(Ti) = 2%. The Fe peak was not detected due to the low Fe content in N/Fe/Zn_TiO
2@BF. The real doping content of N/Fe/Zn_TiO
2@BF obtained through the XPS analysis was the same as the theoretical doping content.
The FT-IR spectra of the synthesized TiO2 and N/Fe/Zn_TiO2 are shown in Fig. 6, which was used to analyze the functional groups of the samples. In Fig. 6(a), the peaks at 3439 cm−1 and 1630 cm−1 were formed by the stretching vibration of the water adsorbed on the surface, ˙OH or the H–OH bond of the COOH group, and the peak at 513 cm−1 was attributed to the characteristic Ti–O bond vibration of TiO2.43,44 In Fig. 6(b), compared with Fig. 6(a), there was a slight offset value at the characteristic peak of TiO2 and the absorption peak of the hydroxyl group. Combined with the results of the XRD and XPS, it indicated that N, Fe and Zn entered into the lattice of TiO2.
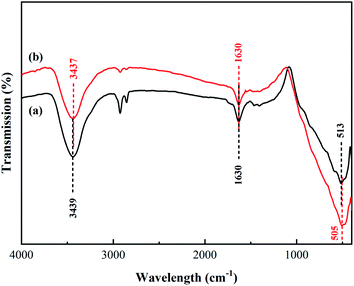 |
| Fig. 6 FT-IR spectra of TiO2 and N/Fe/Zn_TiO2. | |
3.2 Photocatalytic degradation of RhB
As shown in Fig. 7(a), RhB removal by TiO2 (17.93%) alone was a little better than that of TiO2@BF (15.61%), which was due to the TiO2 in TiO2@BF being wrapped, leading to a lower actual amount of the catalyst working in the photocatalysis.
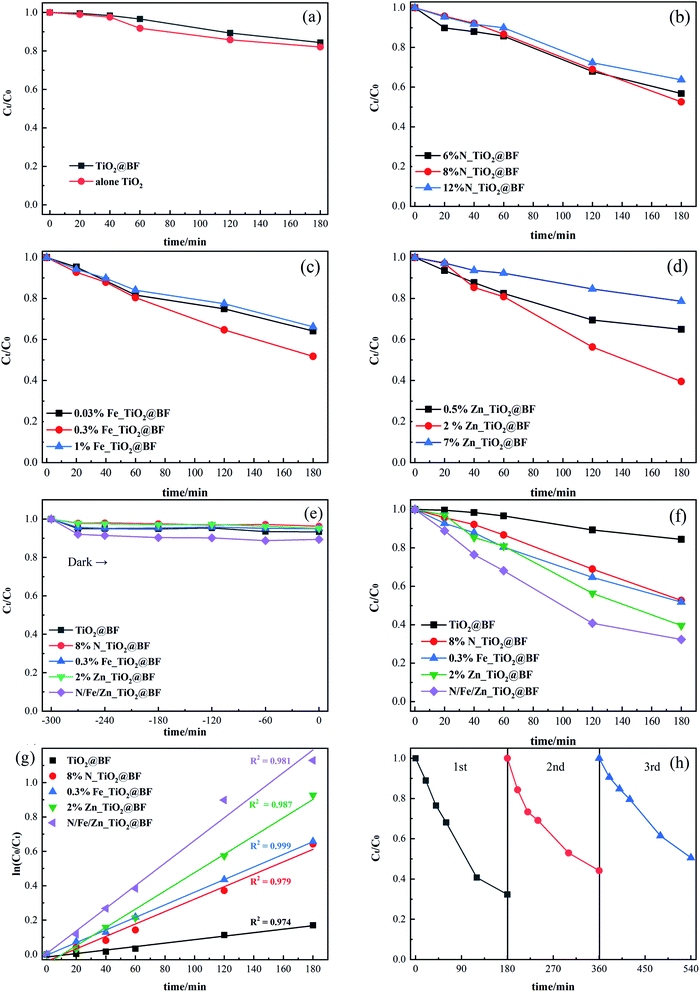 |
| Fig. 7 (a) Photocatalytic activity of the same amount of TiO2 without loading on BF and TiO2@BF, (b–d, f) photocatalytic activities (in the degradation of RhB) of TiO2@BF and G_TiO2@BF doped with different substances at different doping ratios, (e) dark adsorption curves, (g) photocatalytic degradation kinetics and (h) the stability and reusability tests of N/Fe/Zn_TiO2@BF for RhB removal. | |
The photocatalytic activities of three different proportions of TiO2@BF doped with N (N_TiO2@BF), Fe (Fe_TiO2@BF) and Zn (Zn_TiO2@BF) were evaluated as shown in Fig. 7(b–d), which show that when the doping ratios of N, Fe and Zn were 8%, 0.3% and 2%, respectively, the degradation effects of RhB under UV light for 3 hours were the best, reaching 47.40%, 48.20% and 60.45%, respectively. The reason why the degradation efficiency of the 8% N, 0.3% Fe and 2% Zn doping ratios was higher than the 12% N, 1% Fe and 7% Zn doping ratios, respectively, might be that when the doping concentration was too high, the doping substance could not easily enter the TiO2 lattice but instead gathered on the TiO2 surface, reducing the active sites.
Fig. 7(e) illustrates that the adsorption/desorption equilibrium was reached in 30 min. As shown in Fig. 7(f), the photocatalytic activities of N_TiO2@BF, Fe_TiO2@BF, and Zn_TiO2@BF on RhB degradation were all better than that of TiO2@BF under UV light. In particular, the degradation efficiency of RhB by N/Fe/Zn_TiO2@BF as the photocatalytic material was the best (67.67%), 4.33 times that of TiO2@BF, indicating that N, Fe and Zn element doping enhanced the photocatalytic degradation effect, which was consistent with the UV-vis/DRS characterization analysis results.
Fig. 7(g) shows that the photocatalytic degradation of RhB by 8% N_TiO2@BF, 0.3% Fe_TiO2@BF, 2% Zn_TiO2@BF and N/Fe/Zn_TiO2@BF conformed to a quasi-first-order kinetic equation. The degradation rate constant (k) of RhB in different processes and the TiO2 loading amounts for each sample are listed in Table 1. It was found that k8%N_TiO2@BF < k0.3% Fe_TiO2@BF < k2% Zn_TiO2@BF, and the k value of one element dopant of TiO2@BF was greater than the k value of TiO2@BF but less than the k value of N/Fe/Zn_TiO2@BF. The degradation rate constant of N/Fe/Zn_TiO2@BF was 7.04 times that of TiO2@BF, indicating that doping indeed accelerated charge transfer and effectively improved the photocatalytic activity. The analysis result of XRD and RAMAN that the crystallite sizes of N/Fe/Zn_TiO2 were smaller than TiO2 was consistent with this photocatalytic performance.
Table 1 The photo-degradation rate constant and TiO2 loading amounts of different samples
Sample |
Doping ratio |
k × 10−3 (min−1) |
TiO2 loading amount (mg cm−2) |
TiO2@BF |
— |
0.95 |
3.02 |
N_TiO2@BF |
6.00% |
3.07 |
3.11 |
8.00% |
3.59 |
3.08 |
12.00% |
2.50 |
3.08 |
Fe_TiO2@BF |
0.03% |
2.63 |
3.02 |
0.30% |
3.54 |
3.02 |
1.00% |
2.34 |
3.06 |
Zn_TiO2@BF |
0.50% |
2.73 |
3.13 |
2.00% |
4.86 |
3.15 |
7.00% |
1.33 |
3.08 |
N/Fe/Zn_TiO2@BF |
— |
6.69 |
3.04 |
In order to estimate the reusability and stability of N/Fe/Zn_TiO2@BF for RhB removal, three recycling tests were conducted at the same experimental conditions. As shown in Fig. 7(h), the degradation effects of RhB were 67.67%, 55.70% and 55.84% in three consecutive cycle experiments, suggesting that N/Fe/Zn_TiO2@BF could maintain relative stability after the first cycle experiment.
3.3 Degradation mechanism analysis
3.3.1 Optical characteristics and electronic band gaps analysis of the synthesized photocatalyst. As shown in Fig. 8, the optical characteristics and electronic band gaps of TiO2 and G_TiO2 were evaluated by using UV-vis diffuse reflectance. There was an obvious red shift of the absorption band for the N/Fe/Zn_TiO2 photocatalyst compared to TiO2. From the Tauc plot using the Kubelka–Munk function (Fig. 8 inset), the electronic band gaps of the synthesized photocatalysts were in the following order: N/Fe/Zn_TiO2 (2.80 eV) < N_TiO2 (2.85 eV) < Zn_TiO2 (3.03 eV) < Fe_TiO2 (3.08 eV) < TiO2 (3.11 eV). As a result, N/Fe/Zn_TiO2 showed the narrowest energy band gap (2.8 eV) compared to the other synthesized photocatalysts, which meant it was easier to generate electronic transitions under the excitation of UV light, indicating that co-doping of the N, Fe, and Zn elements in this study could have a synergistic effect and improve the photocatalytic activity of N/Fe/Zn_TiO2.
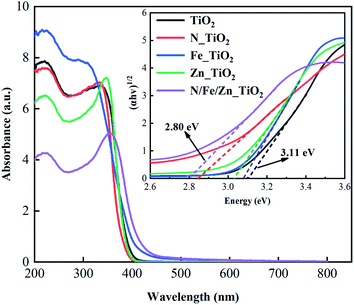 |
| Fig. 8 UV-vis diffuse reflectance spectra of different materials (inset is the band energy spectra). | |
3.3.2 Reactive species quenching experiments. To better elucidate the mechanism of N/Fe/Zn_TiO2@BF for the degradation of rhodamine B, different reactive species quenching experiments were systemically conducted, and the results are presented in Fig. 9. In these experiments, 1.4-benzoquinone (BQ), tert-butyl alcohol (TBA) and EDTA-2Na were used as scavengers,45,46 which had different affinities for different reactive oxygen species, such as the active superoxide radical (˙O2−), hydroxyl radicals(˙OH) and holes (h+). It was observed that the degradation effect of RhB (8.33%) was obviously inhibited by the EDTA-2Na scavenger, which indicated that h+ played a crucial role in this photocatalytic degradation process. When BQ and TBA were added, respectively, the degradation rate of RhB also decreased, suggesting that ˙OH and ˙O2− have an impact on RhB removal. Herein, RhB removal during the treatment process with the BQ scavenger was different from its expected degradation trend. The reason for this result was that some dark colored degradation products of BQ had a positive effect on the determination of RhB by the spectrophotometer method, causing the measured absorbance value to become higher (Fig. 9 inset).
 |
| Fig. 9 Photocatalytic activities (in the degradation of RhB) of N/Fe/Zn_TiO2@BF under the condition of different quenchers (inset is the curve of absorbance and reaction time of the 20 mM BQ without RhB and catalysts). | |
According to the results of the reactive species quenching experiments, it could be inferred that the h+ active species played a dominant role, while ˙O2− and ˙OH were the minor radicals in this photocatalytic system. When N/Fe/Zn_TiO2@BF was illuminated by UV light, electrons (e−) in the valence band (VB) were excited to the conduction band (CB), leaving holes (h+) in the VB, which could directly participate in the RhB degradation (eqn (3) and (4)). Meanwhile, the accumulated e− could capture O2 to obtain ˙O2− (eqn (5)), which could capture H+ generated by the ionization of H2O to form H2O2, and the generated ˙OH might cause the translation of the H2O2 (eqn (7)–(9)).47 The ˙O2− and ˙OH radicals are capable of destroying organic compounds (eqn (6) and (10)).
|
N/Fe/Zn_TiO2@BF + hv → e− + h+
| (3) |
|
h+ + RhB → degradation
| (4) |
|
˙O2− + RhB → degradation
| (6) |
|
˙O2− + 2H+ + e− → H2O2
| (8) |
|
H2O2 + e− → OH− + ˙OH
| (9) |
|
˙OH + RhB → degradation
| (10) |
4 Conclusions
The N/Fe/Zn_TiO2@BF composites were synthesized by a combined sol–gel calcination method. N_TiO2@BF, Fe_TiO2@BF, Zn_TiO2@BF and N/Fe/Zn_TiO2@BF exhibited higher photoactivity towards the degradation of RhB under UV light irradiation compared to TiO2@BF. The degradation efficiency for RhB of N/Fe/Zn_TiO2@BF was 4.3 times that of TiO2@BF, and the degradation process of N/Fe/Zn_TiO2@BF was consistent with first-order kinetics with a k value 7.04 times that of TiO2@BF. The improved photoactivity was attributed to the synergistic effect of the N, Fe and Zn co-doping. The crystallite size of N/Fe/Zn_TiO2 was only 10.4 nm, while that of TiO2 without doping was 18.1 nm. There were more catalytic activity points with the specific surface area of N/Fe/Zn_TiO2@BF increasing greatly, resulting in the improved catalytic efficiency. The results of the EDS, XRD, RAMAN, XPS and FT-IR analysis indicated that the elements of N, Fe and Zn were doped into the crystal lattice of TiO2 without changing the anatase crystalline phase. In addition, N/Fe/Zn_TiO2@BF gained a narrower energy band gap (2.80 eV), which improved the photocatalytic activity. Reactive species quenching experiments indicated that h+ was the most important reactive species and ˙OH and ˙O2− played minor roles for the N/Fe/Zn_TiO2@BF photocatalysis processes in the degradation of RhB.
Conflicts of interest
The authors declare that they have no known competing financial interests or personal relationships that could have appeared to influence the work reported in this paper.
Acknowledgements
This work was supported by the Major Scientific and Technological Special Program of Sichuan Province, China (2018SZDZX0027 and 2019YFS0505) and the Major Science and Technology Application Project of Chengdu City, Sichuan Province, China (2019-YF09-00081-SN).
References
- K. Wetchakun, N. Wetchakun and S. Sakulsermsuk, J. Ind. Eng. Chem., 2019, 71, 19–49 CrossRef CAS.
- L. Jiang, X. Hu, D. Yin, H. Zhang and Z. Yu, Chemosphere, 2011, 82, 822–828 CrossRef CAS.
- K. Lei, Y. Zhu, W. Chen, H. Pan, Y. Cao, X. Zhang and B. Guo, Environ. Int., 2019, 130, 104919 CrossRef CAS.
- A. M. Voigt, P. Ciorba, M. Döhla, M. Exner, C. Felder, E. Sib, D. Skutlarek, R. M. Schmithausen and H. A. Faerber, Int. J. Hyg. Environ. Health, 2020, 224, 113449 CrossRef CAS.
- P. S. Basavarajappa, S. B. Patil, N. Ganganagappa, K. R. Reddy, A. V. Raghu and C. V. Reddy, Int. J. Hydrogen Energy, 2020, 45, 7764–7778 CrossRef CAS.
- J. Zhang, B. Tang and G. Zhao, Appl. Catal., B, 2020, 279, 119364 CrossRef CAS.
- C. Hao, Y. Xu, M. Bao, X. Wang, H. Zhang and T. Li, J. Mater. Sci.: Mater. Electron., 2017, 28, 3119–3127 CrossRef CAS.
- X. Ding, L. Gutierrez, J. P. Croue, M. Li, L. Wang and Y. Wang, Chemosphere, 2020, 253, 126655 CrossRef CAS.
- W. Pronk, A. Ding, E. Morgenroth, N. Derlon, P. Desmond, M. Burkhardt, B. Wu and A. G. Fane, Water Res., 2019, 149, 553–565 CrossRef CAS.
- M. Zhang, F. Xiao, D. Wang, X. Xu and Q. Zhou, Sep. Purif. Technol., 2017, 182, 118–127 CrossRef CAS.
- S. Chen, N. Wang, L. Ma, T. Li, M. Willander, Y. Jie, X. Cao and Z. L. Wang, Adv. Energy Mater., 2016, 6, 1–9 CrossRef CAS.
- J. N. Liu, Z. Chen, Q. Y. Wu, A. Li, H. Y. Hu and C. Yang, Sci. Rep., 2016, 6, 1–9 CrossRef.
- J. R. Kim and E. Kan, J. Environ. Manage., 2016, 180, 94–101 CrossRef CAS.
- F. A. El-Gohary and G. Kamel, Ecol. Eng., 2016, 94, 268–274 CrossRef.
- T. H. Kim, G.-M. Go, H.-B. Cho, Y. Song, C.-G. Lee and Y.-H. Choa, Front. Chem., 2018, 6, 1–10 CrossRef.
- Y. Yan, W. Shi, Z. Yuan, S. He, D. Li, Q. Meng, H. Ji, C. Chen, W. Ma and J. Zhao, J. Am. Chem. Soc., 2017, 139, 2083–2089 CrossRef CAS.
- H. Zong, T. Zhao, G. Zhou, R. Qian, T. Feng and J. H. Pan, Catal. Today, 2019, 335, 252–261 CrossRef CAS.
- A. R. Khataee and M. B. Kasiri, J. Mol. Catal. A: Chem., 2010, 328, 8–26 CrossRef CAS.
- Y. N. Li, Z. Y. Chen, M. Q. Wang, L. zhen Zhang and S. J. Bao, Appl. Surf. Sci., 2018, 440, 229–236 CrossRef CAS.
- L. Kong, Z. Jiang, C. Wang, F. Wan, Y. Li, L. Wu, J. F. Zhi, X. Zhang, S. Chen and Y. Liu, ACS Appl. Mater. Interfaces, 2015, 7, 7752–7758 CrossRef CAS.
- J. Wen, X. Li, W. Liu, Y. Fang, J. Xie and Y. Xu, Chin. J. Catal., 2015, 36, 2049–2070 CrossRef CAS.
- L. Pan, J. J. Zou, X. Zhang and L. Wang, J. Am. Chem. Soc., 2011, 133, 10000–10002 CrossRef CAS.
- J. B. Priebe, J. Radnik, A. J. J. Lennox, M. M. Pohl, M. Karnahl, D. Hollmann, K. Grabow, U. Bentrup, H. Junge, M. Beller and A. Brückner, ACS Catal., 2015, 5, 2137–2148 CrossRef CAS.
- R. Zanella, E. Avella, R. M. Ramírez-Zamora, F. Castillón-Barraza and J. C. Durán-Álvarez, Environ. Technol., 2018, 39, 2353–2364 CrossRef CAS.
- S. Luan, D. Qu, L. An, W. Jiang, X. Gao, S. Hua, X. Miao, Y. Wen and Z. Sun, Sci. Bull., 2018, 63, 683–690 CrossRef CAS.
- R. Lu, Y. Wei, C. Chen and T. Wu, J. Alloys Compd., 2019, 790, 99–108 CrossRef CAS.
- Y. Xiao, X. Sun, linyu Li, J. Chen, S. Zhao, C. Jiang, L. Yang, L. Cheng and S. Cao, Chin. J. Catal., 2019, 40, 765–775 CrossRef CAS.
- A. Mishra, A. Mehta, S. Kainth and S. Basu, J. Alloys Compd., 2018, 764, 406–415 CrossRef CAS.
- E. Rezaei, R. Azar, M. Nemati and B. Predicala, J. Environ. Chem. Eng., 2017, 5, 5902–5911 CrossRef CAS.
- A. Buzarovska, C. Gualandi, A. Parrilli and M. Scandola, Composites, Part B, 2015, 81, 189–195 CrossRef CAS.
- J. M. Wu and Q. E. Zhao, Appl. Surf. Sci., 2020, 527, 146779 CrossRef CAS.
- W. Li and T. Zeng, PLoS One, 2011, 6, 2–7 Search PubMed.
- K. H. Leong, P. Monash, S. Ibrahim and P. Saravanan, Sol. Energy, 2014, 101, 321–332 CrossRef CAS.
- T. Ohsaka, J. Phys. Soc. Jpn., 1980, 48, 1661–1668 CrossRef CAS.
- H. C. Choi, Y. M. Jung and S. Bin Kim, Vib. Spectrosc., 2005, 37, 33–38 CrossRef CAS.
- H. W. Cho, K. L. Liao, J. S. Yang and J. J. Wu, Appl. Surf. Sci., 2018, 440, 125–132 CrossRef CAS.
- Y. Kim, J. Lee, H. Jeong, Y. Lee, M. H. Um, K. M. Jeong, M. K. Yeo and M. Kang, J. Ind. Eng. Chem., 2008, 14, 396–400 CrossRef CAS.
- P. Bharathi, M. Krishna Mohan, V. Shalini, S. Harish, M. Navaneethan, J. Archana, M. Ganesh Kumar, P. Dhivya, S. Ponnusamy, M. Shimomura and Y. Hayakawa, Appl. Surf. Sci., 2020, 499, 143857 CrossRef CAS.
- X. Cheng and L. Yang, Arabian J. Chem., 2016, 9, S1706–S1711 CrossRef CAS.
- M. Sreedhar, I. N. Reddy, P. Bera, D. Ramachandran, K. Gobi Saravanan, A. M. Rabel, C. Anandan, P. Kuppusami and J. Brijitta, Appl. Phys. A: Mater. Sci. Process., 2015, 120, 765–773 CrossRef CAS.
- M. Sreedhar, I. Neelakanta Reddy, C. V. Reddy, J. Shim and J. Brijitta, Mater. Sci. Semicond. Process., 2018, 85, 113–121 CrossRef CAS.
- X. Wang, F. Wang, C. Bo, K. Cheng, J. Wang, J. Zhang and H. Song, Appl. Surf. Sci., 2018, 453, 320–329 CrossRef CAS.
- L. Ma, I. Jia, X. Guo and L. Xiang, Chin. J. Catal., 2014, 35, 108–119 CrossRef CAS.
- Z. He, W. Que, J. Chen, Y. He and G. Wang, J. Phys. Chem. Solids, 2013, 74, 924–928 CrossRef CAS.
- W. Wang, Z. Zeng, G. Zeng, C. Zhang, R. Xiao, C. Zhou, W. Xiong, Y. Yang, L. Lei, Y. Liu, D. Huang, M. Cheng, Y. Yang, Y. Fu, H. Luo and Y. Zhou, Chem. Eng. J., 2019, 378, 122132 CrossRef CAS.
- R. Li, M. Cai, Z. Xie, Q. Zhang, Y. Zeng, H. Liu, G. Liu and W. Lv, Appl. Catal., B, 2019, 244, 974–982 CrossRef CAS.
- W. Wang, Q. Niu, G. Zeng, C. Zhang, D. Huang, B. Shao, C. Zhou, Y. Yang, Y. Liu, H. Guo, W. Xiong, L. Lei, S. Liu, H. Yi, S. Chen and X. Tang, Appl. Catal., B, 2020, 273, 119051 CrossRef CAS.
|
This journal is © The Royal Society of Chemistry 2021 |
Click here to see how this site uses Cookies. View our privacy policy here.