DOI:
10.1039/D2RA01511K
(Review Article)
RSC Adv., 2022,
12, 14137-14153
Research progress and applications of silica-based aerogels – a bibliometric analysis
Received
8th March 2022
, Accepted 2nd May 2022
First published on 11th May 2022
Abstract
Silica aerogels are three-dimensional porous materials that were initially produced in 1931. During the past nearly 90 years, silica aerogels have been applied extensively in many fields. In order to grasp the progress of silica-based aerogels, we utilize bibliometrics and visualization methods to analyze the research hotspots and the application of this important field. Firstly, we collect all the publications on silica-based aerogels and then analyze their research trends and performances by a bibliometric method regarding publication year/citation, country/institute, journals, and keywords. Following this, the major research hotspots of this area with a focus on synthesis, mechanical property regulation, and the applications for thermal insulation, adsorption, and Cherenkov detector radiators are identified and reviewed. Finally, current challenges and directions in the future regarding silica-based aerogels are also proposed.
1. Introduction
Aerogels are a kind of three-dimensional porous material with more than 90% porosity,1 and are often obtained by a sol–gel process,2 fiber accumulation,3,4 or 3D printing.5 Owing to the characteristics of low density and high specific surface area,6 aerogels have been applied in many fields such as thermal insulation,7–9 wastewater treatment,10,11 acoustic insulation,12,13 and drug delivery.14,15 At present, the value of aerogels in blanket and granular form in the global market is estimated at €250 Mio per year, with an annual growth rate as high as ∼20%.16 Within all kinds of aerogels, silica-based aerogels (SAs) have become the most commonly used aerogels. Initially, SAs consist of necklace-like particles which are synthesized through the sol–gel method.17,18 It was firstly introduced by Kistler in 1931 when he used gas to replace the liquid of wet gels to get silica aerogels.19 SAs have not been extensively studied over the next several decades, on account of the complex and time-consuming procedure. It was not until Teichner and Nicoloan produced silica aerogels in 1972, using tetramethyl orthosilicate (TMOS) as a precursor, was the SA produced in a continuous process and obtained through the sol–gel process.20 After the appearance of different technologies, the synthetic process has become diversified. With the introduction of freeze casting and spinning technologies, stacked fibers formed SAs in 2014, and they possess a stronger compressible ability by the transformation of major pores and the densification of minor pores.21–23 Recently, with the development of three-dimensional (3D) printing technology, the combination of 3D printing technology and chemical synthesis provides a new method for the synthesis of SAs in 2020,24 which can manufacture structurally complex products by the design of 3D models and then improve their adaptability in different occasions.25–27 In addition to the above methods, SAs are also produced by deposition on the other aerogels.28 As the most commonly used aerogels, SAs exhibit high-temperature resistance (>800 °C),29,30 low density,31,32 and low thermal conductivity,33 which make them widely used in both civil and military fields. In the military fields, SAs are used to capture hypervelocity particles and protect the primary battery pack of the Alpha Particle X-ray Spectrometer from the influence of low temperatures.34,35 Similarly, SAs are also used as Cherenkov detector radiators to identify the particles.36 In the civil fields, SAs have been used in the insulating bricks, glass fillers,37,38 and adsorption of CO2 and harmful substances.39–42
Owing to the wide exploration and applications of SAs, it is difficult to grasp the research progress of SAs. Thus, we employ the bibliometric analysis method to analyze a large body of SA-related literature, with an aim to obtain their research trend and hotspots. In this study, we first obtain all the research papers in the field of SAs from Web of Science (WoS) Core Collection and identify the publication trends, most contributive countries/regions, institutions, and journals. Meanwhile, research hotspots and main application fields of SAs are also discussed. Specifically, the synthesis of SAs, mechanical property regulation, and their application for thermal insulation, adsorption, and Cherenkov detector radiator are the main research fields. At the end of this review, current challenges and the promising future direction regarding this popular field are also proposed. This study provides a novel strategy to present the research advances and also introduces comprehensive design methods of SAs for different fields, which may serve as a reference review and also accelerate the development of this field.
2. General bibliometrics in terms of publication year, country/institution, and research area
2.1 Data collection and processing method
Bibliometric analysis is a method of analyzing big data based on a large number of documents.43,44 It can depict the publication trend, contributing countries/regions and institutions, and hotspots, which can endow us with a more comprehensive analysis of SAs.45–47 In detail, the data in this study are searched by the search strings of “ts = (SiO2 or silica or “silicon dioxide”) and ts = (aerogel* or xerogel* or cryogel*) not ts = (“silica template*”)” until 12th February 2022 from the WoS Core Collection databases. It is worth noting that aerogels that are studied by us represent gel networks whose liquid was replaced by air. However, they are sometimes named as aerogels, cryogels, and xerogels according to different drying methods: supercritical drying, freeze-drying, and ambient pressure drying (APD), respectively.48,49 Because they all represent the same kind of structure, we search all of their names to represent all gel structures filled with air. In total, there are 151 publications published discontinuously for more than fifty years before 1900, we here only analyzed data after 1900 to reflect the connection between publications and time. A total of 9071 publications are found, with 7937 articles, 268 reviews, 127 meeting abstracts, and other types of publications. Since some document types, such as meeting abstracts and letters, are not frequently cited material, we utilize only articles and reviews in our following analysis.50 In addition, to acquire the application for SAs in many fields, we acquire the research hotspots with the assistance of keywords co-occurrence analysis by Vosviewer. We merge repetitive keywords including their singular and plural forms (i.e., aerogel and aerogels) and their different names, such as SiO2, silica, and silicon dioxide, using thesaurus files.51,52
2.2. Publication trend and contributing countries/regions and institutions
Fig. 1a shows the annual publications and citations from 1990 to 2021. During this period, the number of publications increases as time goes on. Meanwhile, the number of citations also shows an increasing trend year by year. This trend indicates the growing attention among the scientific community to SAs. Owing to their wide application potential, many countries/regions pay efforts on SAs. Hence, the twelve most contributive countries/regions are listed, which are sorted according to the number of total publications (Fig. 1b). China is the most contributive country with 1950 publications. Following are the USA (1497 publications) and France (745 publications). Meanwhile, the index of h represents h publications that were each cited at least h times.53 Thus, the h-index is introduced to reflect the citation performance.54 USA, China, and France exhibit higher h-index, which indicates the publications received higher attention. What's more, from the perspective of institutions, the Chinese Academy of Sciences, with 215 publications, contributes the highest number of publications (Fig. 1c). University of Montpellier 2 (42 h-index) and Université Claude Bernard Lyon 1 (45.92 average citations) have the highest h-index and average citations, respectively.
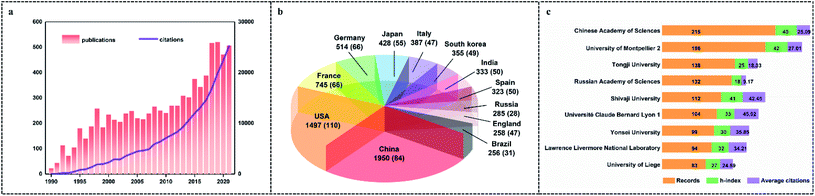 |
| Fig. 1 (a) The trend of publications and citations. (b) The most contributive countries/regions based on the total publication. H-index values appear in the brackets. (c) The most productive institutions based on the total publication. | |
2.3 Bibliographic coupling analysis of referenced sources
Bibliographic coupling analysis of referenced sources could not only identify the most contributive journals but also provide the preliminary information of SAs simply according to the journal names and related-area of journals. As shown in Fig. 2a, the three journals including Journal of Non-Crystalline Solids, Journal of Sol–Gel Science and Technology, and Microporous and Mesoporous Materials receive many SA-related publications. In addition, with the assistance of the identified journals, we could obtain the preliminary information of SAs. For instance, Journal of Non-Crystalline Solids and Ceramics International shows the characteristics of silica such as non-crystal materials and composition of ceramics. Journal of Sol–Gel Science and Technology indicates that they are commonly synthesized by the sol–gel method. Microporous and Mesoporous Materials and Journal of Porous Materials demonstrate their high porosity. Nuclear Instruments Methods in Physics Research Section A: Accelerators, Spectrometers, Detectors and Associated Equipment shows that SAs can be used as Cherenkov detector radiators.
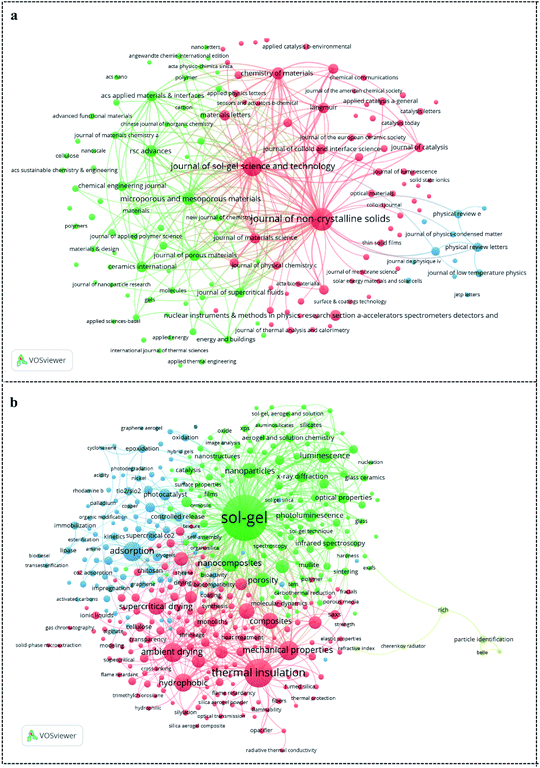 |
| Fig. 2 (a) Bibliographic coupling analysis of referenced sources. The node size represents the number of publications. (b) Keyword co-occurrence analysis with at least 10 occurrences. The node size represents the occurrence frequency of the keywords. | |
2.4. Keyword co-occurrence analysis
After obtaining the general bibliometric information of SAs research, we further utilize keyword co-occurrence analysis to acquire research hotspots of SAs. “Aerogel”, “silica”, “aerogels”, and “silica aerogels”, as the most frequent keywords, but they fail to reveal useful information about SAs. Thus, we remove them from the network to highlight the other keywords.55 Fig. 2b shows the 409 items of keywords co-occurrence analysis (threshold = 10). The larger a circle is, the more frequently a keyword occurs. In addition, Vosviewer is also able to classify keywords into different clusters with different colors, and each cluster presents a similar research field.56 In our dataset, all keywords are divided into four clusters. Specifically, keywords in the green cluster are mainly related to the synthesis and characterization. Keywords in the red cluster are connected with mechanical capacity and thermal insulation. Meanwhile, the blue and yellow clusters mainly reflect the adsorption ability and Cherenkov detector radiator, respectively. Such keywords reveal that the main research hotspots of SAs focus on synthesis, mechanical capacity regulation, and their applications for thermal insulation, adsorption, and Cherenkov detector radiator. In the next section, we will give a brief introduction of each research hotspot of SAs according to our analys.
3. Synthesis technologies
Sol–gel, as a kind of synthesis method of SAs, is the biggest node in the keyword network, which indicates that the synthesis of SAs is the most popular research topic. Consequently, we here summarize different synthesis technologies according to their appearance time (Fig. 3). Here, SAs can be divided into three categories according to different synthesis technologies for different shapes: particulate silica-based aerogels (PSAs), fibrous silica-based aerogels (FSAs), and 3D printing SAs. Initially, SAs consist of necklace-like particles through the sol–gel method and they are named as PSAs.59 Afterward, with the introduction of freeze casting and spinning technologies, stacked fibers were used to form FSAs.60 FSAs have lamellar macrostructure or cellular macrostructure. Recently, 3D printing technology can manufacture structurally complex 3D printing SAs by the design of 3D models.61 Although 3D printing SAs have a similar microstructure to PSAs, the macrostructure of 3D printing SAs can be controllably designed.
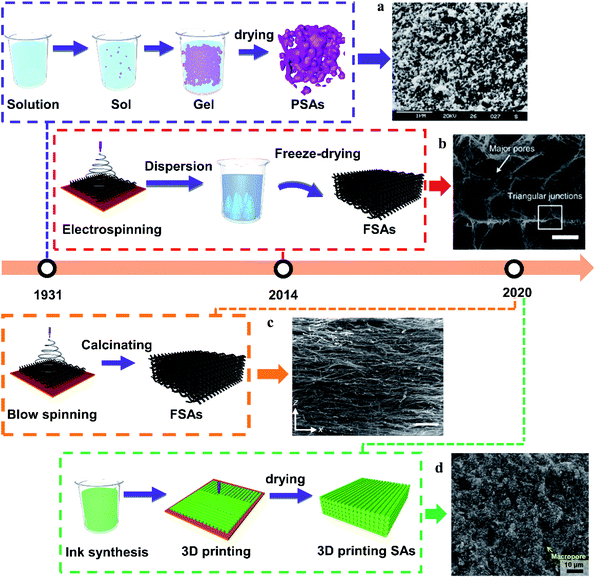 |
| Fig. 3 (a) The representative microscopic image of PSAs Copyright 1999, Elsevier.57 (b) The representative microscopic image of FSAs obtained by ice template method the scale represents 20 μm. Copyright 2020, Springer Nature.21 (c) The representative microscopic image of FSAs obtained by solution blow spinning method. The scale rerepresents 500 μm. Copyright 2020, Springer Nature.22 (d) The representative microscopic image of 3D printing SAs. Copyright 2021, American Chemical Society.58 | |
3.1 PSAs
PSAs are composed of necklace-like silica particles. They are obtained through three steps, respectively are silica wet gels synthesis, aging/modification, and drying.62 Silica wet gels are obtained by the sol–gel method which transforms liquid precursors into a sol to a gel by hydrolysis and condensation reaction.63,64 In the hydrolysis and condensation reaction, primary particles are formed first and then agglomerated into secondary particles. Finally, secondary particles crosslink each other into silica particle networks.65 The silica particle networks and the liquid in the interstices formed silica wet gels. Generally, precursors could be silicates66,67 or silicon alkoxides.57,64,68–71 To accelerate the process of hydrolysis and condensation, different acid or base catalysts were added.72–74 There are many research discussions and summaries regarding the sol–gel process,75–77 so we will not repeat it here.
Aging is a process that precursors continue hydrolysis and condensation,78 which is achieved through the following two processes. One is that silica of particle surface is dissolved and deposited on the necks of gel networks. Another is that small particle is dissolved and precipitated into big particle.79 Both of these processes can increase the strength of the networks and reduce shrinkage and breakage in the subsequent phases. Thus, prolonging aging time or raising the aging temperature can improve the strength and rigidity of the solid skeleton of SAs. Many studies reported that the aging effect depends on the temperature, solvent, concentration, and aging time.80–82 With the increase of time, temperature, and concentration, the process of aging speeds up. Moreover, the rational selection of solvents is also significant to the aging effect.83 For example, Omranpour et al.84 discussed the aging effect in different solvents. The compressive modulus of aerogels, aging in N-hexane, increased 2 and 4 times compared with methanol and water, respectively. Significantly, methanol can inhibit the condensation reaction, which results in a weak effect.
Drying is a process to remove the solvent in silica wet gels, which includes three main methods: APD, freeze-drying, and supercritical drying.85 APD is a drying process under ambient pressure. The wet gels are suffered from capillary stresses because APD is achieved by the transition from liquid to gas phase.86 Because of the capillary stresses during solvent evaporation, SAs obtained by APD were more likely to shrink and break than other drying methods. The capillary stress (Pr) is as follows: Pr = (2γ
cos
θ)/r, where γ is the surface tension of the solution, θ is the contact angle between the solution and the pore wall, and r represents the radius of the pore. Therefore, to minimize shrinkage and breakage, there are three methods to minimize capillary stress. The first method is to exchange the solution of the wet gels with a lower surface tension solution.87,88 The second method is to modify the wet gels with hydrophobic functional groups which endow the gel networks higher contact angle (θ).89,90 Mutual repulsion produced by hydrophobic functional groups can maintain the structural integrity during the process of drying, different from the shrinkage of SAs with hydrophilic functional groups.91–93 For example, Wei et al.33 modified silica aerogels with the hydrophobic group in low surface tension solvent. The as-prepared aerogels have a crack-free structure and volume shrinkage of less than 1%. The third method is to prolong aging time, which endows gel networks with stronger skeletons to withstand capillary stress.94 Next, during the process of freeze-drying, the ice crystals arise from the solution in the wet gels below the freezing point and then are rapidly sublimed under low pressure.95,96 Because of the sublimation process without liquid–gas transition, the wet gels do not suffer from capillary stresses.97 But Scherer et al.98 mentioned that the development of ice crystals can destroy the wet gels in his study, which is easy to cause shrinkage and breakage. Some strategies (such as aging) can increase the strength of the wet gels and then minimize the risk of shrinkage and breakage. Lastly, supercritical drying, which is achieved above the critical point of the solvent by controlling the temperature and pressure, is a drying method that absents the interface between the liquid and the gas phase.99 During the process of supercritical drying, the liquid and the gas phase become a homogeneous supercritical phase, which can avoid capillary stresses.100 However, the drawbacks of supercritical drying are not negligible such as high cost and strict instrument specification.101
3.2 FSAs
FSAs are composed of stacked silica fibers by the ice template or solution blow spinning method.22,102 In terms of the ice template method, it includes three steps: the acquisition and dispersion of silica fibers, freeze casting, and freeze-drying. First, silica fibers which usually are obtained by electrospinning are dispersed.103 To obtain homogeneous structure silica fibers skeletons, silica fibers should be uniformly dispersed in silica sol during the process of freeze casting.104,105 Then, silica fiber skeletons are obtained by the freeze casting process. In this process, owing to the solvent solidifying below freezing point, silica fibers in solution are rejected by ice crystals and then stack each other to form silica fiber skeletons.106,107 Finally, after freeze-drying, the solidified solvent is replaced by air and stacked silica fibers become FSAs. The development condition of ice crystals influences the characteristics of the porosity because the porosity is obtained by the removal of ice crystals porosity. Many studies show that the freezing rate, solvents, additives, and the growth direction of the ice crystals can regulate the morphology of the porosity by influencing the growth of ice crystals.108 It should be noted that the nucleation rate is higher than the crystal growth rate at a low ice solidification rate. It finally results in large ice crystals at a low ice solidification rate, because large ice crystals grow at the cost of smaller ice crystals.109 Conversely, nucleation rate is higher than the ice crystal growth rate faster ice solidification rate at a high ice solidification rate, which can result in small pores and regular structure. For example, Gutiérrez et al.110 obtained aerogels with smaller pore sizes by increasing the freezing rate. Additionally, additives can change the morphology by regulating the growth of ice crystals.111–115 For example, Xian et al.114 prepared aerogels with 30 μm pore size, adding 20 wt% glycerol, while the pore size of aerogels without glycerol was 20–50 μm. It is worth noting that different solvents have been used to produce different types of pore morphologies during the freeze casting of scaffolds and porous ceramics.116,117 For example, Deville et al.118 obtained lamellar pore morphologies during freeze casting in water, while Araki et al.119 produced dendritic pore morphologies during freeze casting in camphor-naphthalene. However, research on the solvent influence for FSAs is still inadequate. Meanwhile, the cellular can be changed by controlling the growth direction of the ice crystals. For example, Si et al.120 prepared FSAs with isotropic cellular structures after unidirectional freezing, while Su et al.23 produced FSAs with anisotropic cellular structures after directional freezing. Different from the PSAs which exhibit weak connections between the particles, the FSAs illustrate stronger compressible ability, which is caused by the transformation of major pores and the densification of minor pores.21 Meanwhile, this phenomenon is also reflected in the relation between relative Young's modulus and relative density. The relative Young's modulus is proportional to relative density to the power of n((E/Es) ∼ (ρ/ρs)n), where ρ and ρs represent the density of the aerogels and the bulk solid materials, while E and Es reveal their Young's modulus. The cellular structure produced by freeze-drying is similar to the structure of wood or honeycomb. This biomimetic structure provides a cellular-dominated mechanical behavior ((E/Es) ∼ (ρ/ρs)2), such as open-cell cellular foams.122,123 Such structure can also endow FSAs with negative Poisson's ratio caused by reversion of the fibrous layer,124 which can bear more stress.125 However, PSAs illustrate inefficient stress transfer among random particulate structures ((E/Es) ∼ (ρ/ρs)3).126 For example, Si et al.120 prepared ceramic nanofibrous aerogels (CNFAs). They obtained silica fibers by electrospinning of silica sol. Silica fibers were homogenized with polyacrylamide solution to become a uniformly dispersed solution. And silica fibers in aluminoborosilicates (AlBSi) and polyacrylamide solution were freeze casting and freeze-drying to obtain composite pre-aerogels (CPAs). After calcined at 900 °C, the adjacent silica fibers of CPAs were connected by AlBSi glass ceramics and then CNFAs were obtained. The stress–strain curve showed that CNFAs can carry the weight over 7000 times of themselves without fracture, and they exhibited 12% plastic deformation loading of 60% compressive strain after 500th cycles. Compared with FSAs with hard bonding points obtained by calcination under high-temperature, FSAs with elastic bonding exhibit stronger compressibility. For example, Wang et al.121 prepared silica nanofibrous (SNF) aerogels which are similar to the juncus pith structure (Fig. 4a). They obtained silica fibers by electrospinning of silica sol. Then the silica fibers were dispersed in hydrolyzed silane sol. The dispersion of the fiber was poured into the model, experiencing freeze casting, and freeze-drying to become silica nanofibrous aerogels. The hydrolyzed silane sol could crosslink with the surface of the fibers to form the Si–O–Si crosslinking networks without high sintering. More importantly, hydrolyzed silane sols with different hydroxyl groups, such as TEOS, MTMS, and DMDMS, have been investigated as crosslinkers (Fig. 4b). The mechanical property measurement showed that SNF/MTMS aerogels did not exhibit plastic deformation, while SNF/TEOS and SNF/DMDMS aerogels exhibited 2% and 10% plastic deformation loading of 50% compressive strain after 5th cycles, respectively (Fig. 4c). It means that the elastic resilience depends on crosslinking degree and flexibility of crosslinkers.
 |
| Fig. 4 (a) Synthetic route of SNF aerogels. (b) Structures of different crosslinking silane coupling agents. (c) Compressive σ versus ε at the 5th loading–unloading cycle of different SNF aerogels.121 Copyright 2020, John Wiley and Sons. (d) Synthetic route of thermal-solidifying SAs.58 Copyright 2021, American Chemical Society. | |
The solution blow spinning is also used to produce FSAs. During the process of solution blow spinning, the inner chamber and the outer chamber connect with silica sol and blow, respectively.127,128 FSAs with a layered structure can be directly produced under pressure drop between the inner chamber and the outer chamber. For example, Jia et al.22 prepared lamellar ceramic aerogels. They obtained Al2O3–SiO2 aerogels by solution blow spinning of alumina-silica sol and calcinating. After adding AlCl3 to the precursor solution, the prepared fibers are easily and stably accumulated into aerogels with lamellar structure rather than random fiber distribution. It could cause Al2O3–SiO2 aerogels to be completely restored to their original shape while the SiO2 aerogels have weak poor compressibility loading of 80% compressive strain along in the direction perpendicular to the stacked layers. The fibers became denser when pressure was loaded and the fibers were rejected by lap joints when pressure was released, which endowed the Al2O3–SiO2 aerogels with high compressibility.
3.3 3D printing SAs
3D printing is an additive manufacturing technique, which deposits materials layer by layer, with the help of computer-aided design technology.24,129,130 Different from the traditional chemical synthesis technologies, 3D printing can manufacture structurally complex products by the design of 3D models. It avoids weak processability and enlarges the application fields of prepared products. 3D printing, especially direct ink writing (DIW),25–27,58,131 are used to produce SAs through three steps: ink synthesis, 3D printing, and drying. DIW needs inks that are non-Newtonian fluids, whose viscosity decreases with the shear rate increases.132,133 In order to obtain SAs, the liquid of 3D printed gels needs to be removed by APD, freeze-drying, or supercritical drying, as discussed above. Zhao et al.25 first prepared pure 3D printing SAs by DIW. They used silica aerogel particles and PPGNH as thickeners to increase viscosity and dispersibility. Ammonia vapor could accelerate the sol–gel process transformation, achieving the solidification of 3D-printing objects. After supercritical drying, 3D printing SAs with high mesoporosity can be implemented. Meanwhile, 3D printing SAs were directly used to protect equipment from overheating. Other solidification methods are proposed because solidification implemented by ammonia vapor is difficult to achieve scale production. For example, Wang et al.58 proposed thermal-solidifying SAs by DIW (Fig. 4d). The ink consisted of PVA solution, urea, silica sol, glycerol, and nanosilica particles. After printing, the thermal solidification of 3D-printing objects was achieved by warming. The hydrogen bond cross-linking effect between PVA and nanosilica powders can regulate rheological properties and form self-supporting structures. The addition of glycerol with a high boiling point and low capillary pressure also avoids the cracks and shrinkage caused by volatilization. The thermal solidification was achieved through the hydrolysis of urea. The hydrolysate of urea is alkaline in solution, which could accelerate sol–gel progress. Finally, 3D printing SAs with abundant mesopores were produced after supercritical drying. In addition to this, freeze casting, as a solidification method, has been used in the process of other aerogels. For example, Kam et al.134 fabricated cellulose nanocrystals aerogels which were solidified by freeze casting. Xyloglucan was a binder and controlled the rheology. During the process of 3D printing, the material was extruded on a cold platform to achieve solidification by freeze casting. In order to simultaneously conduct printing and freeze casting, the temperature was manually controlled to ensure that two top layers were unfrozen and others frozen. Although freeze casting has not been used in the solidification of SAs, combining freeze casting and a more intelligent temperature control system has the potential to become a scale production method. Meanwhile, with the assistance of freeze casting, Newtonian inks can be used to prepare aerogels.135 For example, Yan et al.5 prepared Ag nanowire aerogels using inkjet printing, which were solidified by freeze casting solution. After low viscous Ag nanowire suspension was deposited on the cold plate whose temperature was −30 °C, the suspension was frozen layer by layer and eventually formed aerogels.
4. Mechanical property regulation
The mechanical property is the second-largest node in the red cluster of the keyword network, which indicates that the mechanical property regulation of SAs, especially PSAs, plays an important part in the process of machining. Because the pure PSAs are composed of necklace-like silica particles. The connection points between silica are Si–O–Si bondings which are stiffbonds.65,136 It means that their connection between particles is weak and pure PSAs are fragile materials. When forces act on it, pure PSAs tend to crack, which was adverse to subsequent processing, limiting their applications.137 However, FSAs possess the stronger compressible ability which is achieved by the transformation of major pores and the densification of minor pores.138 Similarly, 3D printing SAs are produced according to designed 3D models, which avoids subsequent processing after manufacture and decreases the possibility of cracking.25 Thus, to make the best of SAs, improving their mechanical property is indispensable. The strategies are listed as follows: cross-linking and adding reinforcing phases.
4.1 Cross-linking
Another strategy is cross-linking with polymers which could form extra chemical bonds between silica particles.139 For example, Jiang et al.140 added triethoxysilane-grafted polyrotaxane in the hydrolyzed TEOS sols to obtain wet gels. The drying process was achieved by supercritical drying. With the increase of triethoxysilane-grafted polyrotaxane content, the gelling time became shorter. This phenomenon illustrated that polyrotaxane chains can cross-link silica particles and form a “pearl-necklace-type” structure. This structure resulted in 2 orders of magnitude compression strength compared with pure SAs. It was worth noting that prepared SAs showed the same porosity as pure SAs. In another study, Meador et al.141 prepared epoxy crosslinked SAs. TMOS and (aminopropyl)triethoxysilane (APTES) were chosen as the precursors of wet gels. Epoxy cross-linkers with different numbers of functional epoxide could crosslink with the amines on the surface of silica. The mechanical test suggested that the stress at breakpoint and modulus of as-prepared SAs which were cross-linked with different numbers of functional epoxide both increase by as much as 2 orders of magnitude. It should be noted that the SAs cross-linked with trifunctional epoxide exhibited the strongest stress at breakpoint and modulus. The cause of the phenomenon is that as the number of epoxy groups increases, the molecules may become too constrained to increase reactive sites.
4.2 Adding reinforcing phases
Adding reinforcing phases can disperse and divert the external forces over the entire SAs to reinforcing phases, which is also an effective strategy to enhance the robustness of SAs.142 Owing to the high toughness or compressibility of carbon nanotubes (CNT),143 graphenes, fibers,144 and polymer skeleton,71 they are often used as reinforcing phases. For example, He et al.145 prepared bacterial cellulose aerogels/silica aerogels. The dispersed bacterial cellulose fibers formed a three-dimensional skeleton via freeze-casting and were impregnated to silica sols under vacuum. With the hydrolysis and condensation of silica sols, the silica aerogels gradually formed as fillers. The bacterial cellulose aerogels/silica aerogels could bear a compressive strain up to 80% and recover to their original volume after the release of the stress. More importantly, the maximum stress was 25.6 kPa at 50% strain and no significant decrease in maximum stress at 50 cyclic compressions. In another study, Lamy-Mendes et al.143 prepared CNT-silica aerogels composites. HNO3 was for the first time used to form oxygen functional groups on CNT, which is easy to modify with Methyltrimethoxysilane (MTOS) on CNT. The hexadecyltrimethylammonium bromide which can disperse CNT in base solution and control the microstructure of the silica aerogels and MTOS-CNT were added to the solvent. Then Methyltrimethoxysilane (MTMS) and (3-aminopropyl)trimethoxysilane (APTMS), as the precursors, were added into the solvent, which formed silica networks under acid and basic catalyst. The CNT-silica aerogels composites were obtained after aging and APD. The uniaxial compression measurement showed the addition of CNT increased the hardness of CNT-silica aerogels. Meanwhile, Young's modulus increased when CNT or/and APTMS were added, suggesting the reinforcing effect of reinforcing phases.
5. Applications of SAs
5.1 Thermal insulation
Thermal insulation is the biggest node in the red cluster and the second-largest node in the keyword network, indicating that SAs have a low total thermal conductivity and are mainly used for thermal insulation. Because of the small porosity of SAs (<4 mm), convection heat transfer is ignorable.146 Thus, the total thermal conductivity (λtoal) of SAs is composed of solid heat transfer (ksolid), air heat transfer (kgas), and radiation heat transfer (kr).147 The total thermal conductivity is as follows: λtoal = ksolid + kgas + kr. Owing to the low density and porosity of SAs, SAs have the potential to be thermal insulation materials. At the same time, the application of SAs in thermal insulation gradually expands from the military field to the civil field. For example, for the first time since 1997, SAs were firstly used as insulators on the Mars Rover, as a part of the Pathfinder mission to protect the primary battery pack of the Alpha Particle X-ray Spectrometer from the influence of low temperatures.148 In addition, SAs are used as thermal insulation coating for space suits.149 With the development of SAs, they were applied in civil fields such as a building. For example, Wernerywe et al.38 prepared an aerogels-filled insulating brick. The thermal conductivity of them decreased by 35%, compared with commercially perlite filling brick. It means that we can use thinner insulating bricks to achieve high thermal insulation, which could greatly improve building usage space. Furthermore, based on the promising potential of SAs in the thermal insulation field, many methods were developed to further decrease the thermal conductivity of SAs. Next, we discuss the strategies for reducing thermal conductivity by regulating solid heat transfer, air heat transfer, and radiation heat transfer.
Solid heat transfer is a way to transfer heat through the solid network. During the process of solid heat transfer, heat transfer is realized in the form of free electrons and phonons.150 For silica, the phonons heat transfer is the main way in solid heat transfer and is achieved by forceful lattice vibration and the transmission between adjacent units.151,152 The interface between gas and solid generates strong boundary scatterings, which can effectively inhibit the transfer of phonons and then reduce the solid heat transfer.153 This process can be achieved by regulating structure.23 For example, Jia et al.22 prepared lamellar ceramic aerogels. The air within and between stacked layers can effectively decrease solid heat transfer in the direction perpendicular to the stacked layers. And owing to the tortuous and convoluted solid networks, solid heat transfer was limited. Compared with the thermal conductivity in the direction perpendicular to the stacked layers, the Al2O3–SiO2 aerogels had lower thermal conductivity as low as 0.034 Wm−1 K−1 in the direction parallel to the stacked layers (Fig. 5a–c). Therefore, we can adjust the structure of SAs to obtain anisotropic materials with extremely low thermal conductivity in a certain direction.
 |
| Fig. 5 (a) The thermal insulation performance of Al2O3–SiO2 aerogels at high temperature. (b) The thermal conductivity of Al2O3–SiO2 aerogels at different densities. (c) The thermal conductivity of the Al2O3–SiO2 aerogels with a density of 16 mg cm−3.22 Copyright 2020, Springer Nature. (d) The inhibition of air heat transfer by decreasing pore size.157 Copyright 2017, Elsevier. (e) The mechanism of adding opacifier for inhibiting thermal insulation.159 Copyright 2021, Elsevier. | |
Air heat transfer is a way to transfer heat through the collision of air molecules with each other and the solid networks.154 Because the mean free path of air molecules is 70 nm under ambient conditions, the air heat transfer is constant when the pore size of SAs is more than 70 nm. When the pore size is below 70 nm, the air heat transfer is restricted according to the Knudsen effect.155,156 Thus, it is an effective method to suppress air heat transfer by reducing the pore size of SAs (Fig. 5d).157 For example, Dou et al.158 prepared binary-network structured silica aerogels. The silica fibers obtained by electrospinning were dispersed in a hydrolyzed silane sol for freeze casting and freeze-drying. After calcined at 700 °C, silica fibrous aerogels were obtained. The prepared silica fibrous aerogels were immersed into MTMS-based silica sol. During the hydrolysis and condensation reaction, the binary-network gels could be formed. Finally, binary-network structured silica aerogels were obtained after the APD and calcination at 800 °C. The thermal conductivity test showed when the mass of MTMS increased to 0.5 g, the thermal conductivity decreased to 21.96 mWm−1 K−1 at ambient temperature, while thermal conductivity without adding of MTMS is more than 25 mWm−1 K−1. This phenomenon is caused by the average pore size change from 34.22 nm to 3.41 nm, with the content of MTMS increased to 0.5 g. The decrease of average pore size limits the collisions of gas molecules, which effectively decreased thermal conductivity by suppressing air heat transfer. However, when the content of MTMS increases to 2 g, the thermal conductivity is more than 26 mWm−1 K−1. This is related to the higher solid heat transfer caused by greater bulk density, despite the small pore size (6.09 nm). As a result, the proper content of silica sol can inhibit the thermal conductivity by suppressing air heat transfer.
Radiation heat transfer is a way to transfer heat through electromagnetic waves, which exist in the form of infrared radiation.160 However, pure SAs are transparent in the infrared wavelength range between 3 and 8 μm.161 Meanwhile, radiation heat transfer will increase as the temperature grows. Therefore, adding opacifiers with high infrared radiation scattering or absorption ability (such as TiO2,159 graphene,162 and Y2O3 (ref. 163)) can effectively reduce the radiation heat transfer to inhibit thermal conductivity (Fig. 5e). For example, Zhu et al.162 prepared graphene-doped silica aerogels. They added graphene into hydrolyzed silica sol and then added a base catalyst to form graphene-doped silica wet gels. After the aging and supercritical drying, graphene-doped silica aerogels were obtained. The thermal conductivity test showed the thermal conductivity decreased from 0.030 to 0.0184 Wm−1 K−1, with the increase of the content of graphene from 0 to 0.10 wt%, at ambient temperature. This was caused by the uniform dispersion of graphene in silica aerogels, which reduced radiation heat transfer and had no contribution to the solid heat transfer. When the content of graphene continues to increase to 0.15 wt%, the thermal conductivity increased to 0.0191 Wm−1 K−1. A mass of graphene connected each other, which made a greater impact on solid heat transfer than radiation heat transfer. Thus, the thermal conductivity can be controlled by adding opacifiers.
5.2 Adsorption
The blue cluster in the keyword network shows the application of SAs for adsorption. The adsorption is the most frequent keyword in the blue cluster, which reflects the common feature of these applications. Other keywords such as copper, rhodamine B, and CO2 adsorption illustrated the adsorption for heavy metal ions, oil and organic dyes, and CO2. As a global issue, water pollution is a health risk due to its damage to humans and the environment. Heavy metal ions in water pollution can damage the liver, kidneys and even cause cancer.164 Thus, taking proper strategy to remove heavy metal ions in water pollution is indispensable. The SAs possess small pores and large surface areas, which can provide a mass of adsorption sites.165,166 Meanwhile, they are easily surface modified to meet different needs for adsorption.167 These characteristics are in favor of adsorption and make them available in wastewater treatment. In general, the process of adsorption is related to electrostatic interactions, hydrogen bonds, or chelate effects.175 The effect of adsorption for heavy metal ions was influenced by (1) pH, (2) temperature, (3) time, (4) type of ions, (5) initial concentration of ions, (6) the content of SAs, and (7) surface functionalization.176,177 At the different pH, the surface charges of aerogels are influenced. With the increase of pH, a stronger adsorption ability was exhibited, which can attribute to the more negative surface charge on aerogels. In general, the adsorption effect of heavy metal ions is proportional to temperature. The rapid diffusion of heavy metal ions at a high temperature promotes the adsorption effect. However, a lower temperature favor adsorption when the process of adsorption is an exothermal reaction. The heavy metal ions are gradually adsorbed along with time, until reach equilibrium. The rate of adsorption gradually decreases, because of more available adsorption sites at the beginning. Same aerogels produce different effects on the different types of ions, which can attribute to the different interactions between functional groups and ions. The higher the initial concentration of ions, the higher the adsorption efficiency. With the increase of the content of SAs, more heavy metal ions are removed, due to a mass of available exchangeable sites caused by the high surface area. Surface functionalization of silica aerogels can enhance the chelate effect for heavy metal ions (such as sulfhydryl,171,178 carboxyl,179 and amino group180,181). Different surface-modified SAs adsorbents and their adsorption condition of heavy metal ions are summarized in Table 1.
Table 1 Different surface-modified SAs adsorbents and their adsorption condition. R: range, O: optimum, E: equilibrium
Functionalization |
Heavy metal ions |
The initial concentration of ions |
pH |
Time |
The content of SAs |
Temperature |
Ref. |
Mercaptopropyl trimethoxysilane (MPTMS) |
Cd2+ |
R 50–400 mg mL−1 |
R 2–7 |
R 10–60 min |
R 0.02–0.12 g |
|
168 |
O 50 mg mL−1 |
O 6 |
E 30 min |
O 0.05 g |
Pb2+ |
R 50–400 mg mL−1 |
R 2–7 |
R 10–60 min |
R 0.02–0.12 g |
O 50 mg mL−1 |
O 6 |
E 30 min |
O 0.05 g |
Cu2+ |
R 50–400 mg mL−1 |
R 2–7 |
R 10–60 min |
R 0.02–0.12 g |
O 50 mg mL−1 |
O 4 |
E 30 min |
O 0.1 g |
4-Amino-5-methyl-1,2,4-triazole-3(4H)-thion (AMTT) |
Hg2+ |
|
R 2–11 |
R 5 min-20 h |
R 0.01–0.1 g |
R 20, 35, 45, and 60 °C |
169 |
O 6 |
E 8 h |
O 0.06 g |
E 20 °C |
APTES |
Cu2+ |
R 50–500 mg mL−1 |
R 2–12 |
R 0–48 h |
R 0.05–1.6 g |
|
170 |
O 500 mg mL−1 |
O 6 |
E 24 h |
O 0.05 g |
Ni2+ |
R 50–500 mg mL−1 |
R 2–12 |
R 0–8 h |
R 0.05–1.6 g |
O 500 mg mL−1 |
O 6 |
E 5 h |
O 0.05 g |
MPTMS |
Hg2+ |
|
R 2–7 |
R 0–6 h |
R 0.05–1.25 mg mL−1 |
|
171 |
O 6 |
E 1 h |
O 0.5 mg mL−1 |
Cu2+ |
R 2–7 |
R 0–6 h |
R 0.2–5 mg mL−1 |
O 4 |
E 2 h |
O 2 mg mL−1 |
Activated carbon |
Pb2+ |
R 10–300 mg mL−1 |
R 2–7 |
R 0–60 min |
R 20–500 mg |
R 20, 35, 45, and 60 °C |
172 |
O 10 mg mL−1 |
O 6 |
E 30 min |
O 500 mg |
E 60 °C |
Iron(III)chloride hexahydrate (FeCl3·6H2O), iron(II)chloride tetrahydrate (FeCl2·4H2O), and chitosan (CS) |
Cd2+ |
|
R 3–8 |
R 0–600 min |
R 0.005 to 0.03 g |
|
173 |
O 8 |
E 120 min |
O 0.02 g |
Gelatin |
Hg2+ |
|
R 3–7 |
R 5–120 min |
|
|
174 |
O 6 |
E 15 min |
Besides heavy metal ions, oil and organic dyes in water pollution also raise considerable concerns. Hydrophobic and hydrophilic modification on the surface of SAs have been used to oil and organic dyes adsorption, respectively.182–186 For example, Chen et al.187 prepared hydroxyl modified SAs to adsorb Congo red (CR) and Methyl blue (MB) (Fig. 6a). The pHPZC of hydroxyl modified SAs was 5.8. When the pH of the solution was higher than 5.8, the negative charges on the surface of them promoted MB adsorption. When the pH of the solution was lower than 5.8, the positive charges on the surface promoted the CR adsorption. Thus, the removal rate of MB and CR are both more than 90% at pH 9 and 4, respectively. This is because MB and CR are cationic and anionic dyes, respectively. Meanwhile, hydrophobic SAs can easily be infiltrated by oil with low surface tension values, which is in favor of adsorption for oil. For example, Selay et al.189 prepared different surface-modified SAs to adsorb oil. The TMCS, as a surface-modified silane, endowed SAs with the highest surface area value (798 m2 g−1) and superhydrophobicity (θ = 152°). MTMS-modified and MEMO-modified SAs had different surface area values (528 and 223 m2 g−1), and their contact angle values were 142° and 120°, respectively. These characteristics lead to the adsorption capacity of TMCS-modified SAs for kerosene and diesel oil being 12.5 g g−1 and 11.6 g g−1, while MTMS-modified SAs was 8.1 g g−1 and 8.7 g g−1, respectively.
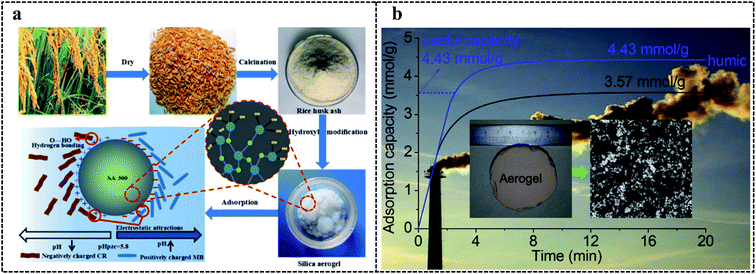 |
| Fig. 6 (a) The adsorption of hydroxyl modified SAs for CR and MB.187 Copyright 2021, Elsevier. (b) The adsorption of RF/SiO2 aerogels for CO2.188 Copyright 2015, Elsevier. | |
Excessive CO2 emission is an important factor contributing to global warming, which means the adsorption of CO2 is indispensable. The high porosity of SAs endows them with high adsorption ability. The high selectivity of the amino groups for CO2 also offers the opportunity for selectively adsorption of amino-modified SAs for CO2.190 For example, Linneen et al.191 prepared SAs which were grafted by silane with different amounts of amine units. The CO2 adsorption ability gradually increased with the increased number of amine units. This phenomenon was caused by the absorbability of amine units for CO2. Meanwhile, the humidity was verified to be a positive factor for CO2 adsorption. For example, Kong et al.188 prepared RF/SiO2 aerogels, and APTES was used as a precursor to endow aerogels with amine groups (Fig. 6b). The total CO2 adsorption ability of RF/SiO2 aerogels at 30 °C under dry and humid 1% CO2 was 3.57 and 4.43 mmol g−1, which indicated the favorable adsorption under humid conditions. Excitedly, after 50 cyclic adsorption–desorption tests, the adsorption ability decreased from 4.43 to 4.29 mmol g−1 and from 3.57 to 3.51 mmol g−1, under dry and humid conditions, respectively. This strong cycling stability was caused by the stability of chemically modified amine groups, different from the weak cycling stability of physically modified amine groups which was caused by the consumption of physically modified amine groups under humidity conditions. Except for humidity, temperature is another influencing factor for CO2 adsorption. For example, Zhao et al.192 prepared tetraethylenepentamine-functionalized silica foam. When the temperature increased from 30 °C to 75 °C, the CO2 adsorption ability gradually increased to 4.75 mmol g−1, which was caused by the improved CO2 diffusion with the increase of temperature. However, the CO2 adsorption ability gradually decreased with the increase of temperature from 75 °C to 105 °C, which is due to the fact that the reaction between CO2 and amine groups was exothermic. Thus, the adsorption was transformed into thermodynamic control when the temperature exceeded 75 °C, indicating that the high temperature was adverse to adsorption. In addition to amino-modified SAs, SAs loading sorbents such as K2CO3 also showed high CO2 adsorption performance. For example, Guo et al.193 impregnated silica wet gels in K2CO3 ethanol solution to obtain K2CO3 loaded SAs and the CO2 adsorption measurement was conducted under the 1% CO2 and 2% H2O at 20 °C. The maximum CO2 capture ability and K2CO3 utilization efficiency achieve 1.32 mmol CO2/g and 88.62% at 20 wt% K2CO3, respectively.
5.3 Cherenkov detector radiator
The yellow cluster in the keywords network shows the application for Cherenkov detector radiator. The frequent keywords in this cluster are Cherenkov radiator, RICH (ring imaging Cherenkov), BELLE, and particle identification, which shows that they are installed on Cherenkov detector as Cherenkov detector radiators to achieve particle identification. When the movement velocity of a charged particle in a medium is faster than the speed of light in this medium, Cherenkov radiation can be produced.194 Thus, particle identification can be achieved by measuring their velocity and momentum according to Cherenkov radiation.195 SAs were used as radiators by virtue of their low refractive index and high transparency. At present, they have been applied in threshold Cherenkov counters and RICH counters.196,197 These two kinds of Cherenkov counters identified particles in different forms: one showed particles that exceeded the threshold,198 the other distinguished particles by the position of the circular image.199 For example, Adachi et al.200 utilized a threshold Cherenkov counter equipped with silica aerogels to identify π and K. Owing to the low refractive index (1.013) of silica aerogels, identifying particles whose momentum in the 1.0–2.5 GeV/c range was adequate. The high transparency of silica aerogels can compensate for low photon yield by increasing thickness. After the diffuse scattering system collected light and fine-mesh type photomultipliers improved the viability of readout, the distinguish efficiency of π and K was greater than 90%. Similarly, Bellunato et al.201 utilized a RICH detector equipped with silica aerogels whose refractive index were 1.0306 and 1.0298 to identify π and P. The test results showed that π and P were distinguished when the momentum was in the 6–10 GeV/c range.
5.4 Other applications
In addition to the above-mentioned applications from the keyword network, SAs are also widely used in other fields, such as catalyst carriers, drug delivery, and optical devices.
SAs have the characteristics of high specific surface area and high porosity, which endows them as catalyst carriers.202–204 Compared with catalysts alone, catalysts loaded on SAs not only improved stability but also are easier to facile recovery and reuse.205,206 For example, Lisboa et al.207 loaded lipase onto SAs. After incubation at 40 °C for 6 days, free lipase was inactivated, while the activity of lipase loaded on SAs was more than 50%. The conversion rate reached 70% when they were placed in an organic medium for 144 h at 40 °C. Meanwhile, because the biocompatibility of silica particles has been widely researched and has shown high biocompatibility, SAs are also used for drug delivery.208,209 SAs can load drugs with low water solubility to improve drug delivery at the site.210–212 For example, Smirnova et al.213 loaded the low soluble drugs, such as ketoprofen and griseofulvin, onto hydrophilic silica aerogels by supercritical CO2. Owing to the collapse of hydrophilic aerogels in liquids, the dissolution rate of drugs is quickly enhanced in liquids, which improves the bioavailability of low soluble drugs. In addition, with the low refractive index and high transparency, SAs have been introduced into the optical fiber214,215 and laser glass.216
6. Conclusions
So far, SAs have been applied extensively in many fields. With the assistance of bibliometric analysis, we identify and analyze research hotspots including SA synthesis, mechanical property regulation, and their applications for thermal insulation, adsorption, and Cherenkov detector radiators. According to different synthesis technologies for different shapes, SAs are divided into three categories: PSAs, FSAs, and 3D printing SAs. Because the PSAs are composed of necklace-like silica particles through the sol–gel process. The connection points between silica are weak. It means that PSAs are easy to crack in the subsequent processing and use, which limits their applications. After the introduction of freeze casting and spinning technologies, stacked fibers accumulate into PSAs. The transformation of major pores and the densification of minor pores endow FSAs with a stronger compressible ability. It means that FSAs have good processibility. Recently, 3D printing technology is used to produce 3D printing SAs. 3D printing SAs are manufactured in the desired shape, which decreases subsequent processing and the possibility of cracking. Thus, to improve their processibility, some strategies are adopted to improve mechanical properties including prolonging aging time, cross-linking, and adding reinforcing phases. Next, we discuss the application of SAs for thermal insulation, adsorption, and Cherenkov detector radiator. Owing to their low density and porosity, SAs have the potential to be thermal insulation materials. Meanwhile, the thermal conductivity can be further decreased by regulating the structure, reducing the pore size, and adding opacifiers with high infrared radiation scattering or absorption ability. Easily modified structure and a mass of adsorption sites brought by large surface areas endow them with adsorption ability. Their adsorption ability is applied in adsorption for heavy metal ions, oil, organic dyes, and CO2. They can also be applied as Cherenkov detector radiators. However, despite the extensive study of SAs, there are still many challenges and opportunities in the future as follows.
(1) Eco-friendly synthesis is critical to environmental pollution and the health of operators. Thus, in the process of preparation for SAs, how to use green and pollution-free reagents to obtain SAs needs to be considered. It is worth noting that the burning of rice paddy generates a mass of rice husk ash every year. In recent years, rice husk ash, as a non-toxic silicon source, is used as a precursor to producing SAs.217,218 However, the solvent in the synthesis and aging process is usually poisonous and volatile, which results in serious environmental pollution. How to design a synthetic method, using a non-toxic solvent in the process of synthesis and aging, is need to be further explored.
(2) In processing and real applications, SAs could be subjected to a variety of stresses. However, many studies focused on the enhancement of hardness and compressibility performance. Other bearing conditions, such as twist and bend, are not discussed. Thus, other bearing conditions of SAs should be measured and improved to meet different work situations.
(3) With the development of 3D printing, we can manufacture structurally different products. However, computer techniques such as simulation have not been applied to design the structure of SAs. For example, the finite element method was used to simulate the total deformation ability of products with different structures.219 According to the deformation and stress distribution region obtained by the simulation, we can determine the structure with the best mechanical properties and deformation ability. It means that using these techniques, we can design the structure with better capability (such as compression performance and thermal insulation) to meet different needs.
(4) 3D printing technology can directly produce 3D printing objects from a computer-aided design model, which endows them with potential for mass manufacturing. However, 3D printing objects need to be solidified to maintain an original shape after 3D printing, and the research on the solidification methods is not enough. From the perspective of large-scale preparation of SAs, thermal solidification is an effective solidification method. In addition to this, freeze casting is a feasible method to produce other aerogels though it has been not used to produce 3D printing SAs. Combining freeze casting and a more intelligent temperature control system has the potential to become a scale production method. Meanwhile, freeze casting allows Newtonian fluid as ink, which enlarges the variety of inks.
Author contributions
Chao Ji: Methodology, Data curation, Formal analysis, Software, Visualization, Writing - original draft. Shuang Zhu: Methodology, Software, Formal analysis, Writing - review & editing. Enshuang Zhang: Methodology, Data Curation, Writing – review & editing. Wenjing Li: Methodology, Writing – review & editing. Yuanyuan Liu: Methodology, Writing – review & editing. Wanlin Zhang: Writing – review & editing. Chunjian Su: Methodology, Writing – review & draft, Supervision. Zhanjun Gu: Methodology, Writing – review & draft, Supervision, Funding acquisition. Hao Zhang: Resources, Writing – review & draft, Supervision, Funding acquisition.
Conflicts of interest
“There are no conflicts to declare”.
Acknowledgements
This work was supported by Strategic Priority Research Program of Chinese Academy of Sciences [XDB36000000]; National Basic Research Program of China [2020YFA0710702 and 2021YFA1201200]; National Natural Science Foundation of China [52075510]; Directional Institutionalized Scientific Research Platform relies on Beijing Synchrotron Radiation Facility of Chinese Academy of Sciences; and Beijing Natural Science Foundation [2222087].
Notes and references
- D. W. Schaefer and K. D. Keefer, Phys. Rev. Lett., 1986, 56, 2199–2202 CrossRef CAS PubMed.
- I. Smirnova and P. Gurikov, J. Supercrit. Fluids, 2018, 134, 228–233 CrossRef CAS.
- L. Cao, Y. Si, X. Yin, J. Yu and B. Ding, ACS Appl. Mater. Interfaces, 2019, 11, 35333–35342 CrossRef CAS PubMed.
- C. Wang, X. Chen, B. Wang, M. Huang, B. Wang, Y. Jiang and R. S. Ruoff, ACS Nano, 2018, 12, 5816–5825 CrossRef CAS PubMed.
- P. Yan, E. Brown, Q. Su, J. Li, J. Wang, C. Xu, C. Zhou and D. Lin, Small, 2017, 13, 1701756 CrossRef PubMed.
- N. Hüsing and U. Schubert, Angew. Chem., Int. Ed., 1998, 37, 22–45 CrossRef.
- M. Reim, W. Körner, J. Manara, S. Korder, M. Arduini-Schuster, H.-P. Ebert and J. Fricke, Sol. Energy, 2005, 79, 131–139 CrossRef CAS.
- B. E. Yoldas, M. J. Annen and J. Bostaph, Chem. Mater., 2000, 12, 2475–2484 CrossRef CAS.
- E. Zhang, W. Zhang, T. lv, J. Li, J. Dai, F. Zhang, Y. Zhao, J. Yang, W. Li and H. Zhang, ACS Appl. Mater. Interfaces, 2021, 13, 20548–20558 CrossRef CAS PubMed.
- E. Hu, X. Wu, S. Shang, X.-m. Tao, S.-x. Jiang and L. Gan, J. Cleaner Prod., 2016, 112, 4710–4718 CrossRef CAS.
- X. Ye, S. Shang, Y. Zhao, S. Cui, Y. Zhong and L. Huang, Cellulose, 2021, 28, 7201–7212 CrossRef CAS.
- S. Takeshita, S. Akasaka and S. Yoda, Mater. Lett., 2019, 254, 258–261 CrossRef CAS.
- K. Wu, W. Dong, Y. Pan, J. Cao, Y. Zhang and D. Long, Ind. Eng. Chem. Res., 2021, 60, 1241–1249 CrossRef CAS.
- C. A. García-González, M. Jin, J. Gerth, C. Alvarez-Lorenzo and I. Smirnova, Carbohydr. Polym., 2015, 117, 797–806 CrossRef PubMed.
- J. Zhao, C. Lu, X. He, X. Zhang, W. Zhang and X. Zhang, ACS Appl. Mater. Interfaces, 2015, 7, 2607–2615 CrossRef CAS PubMed.
- S. Zhao, W. J. Malfait, N. Guerrero-Alburquerque, M. M. Koebel and G. Nyström, Angew. Chem., Int. Ed., 2018, 57, 7580–7608 CrossRef CAS PubMed.
- S. D. Bhagat and A. V. Rao, Appl. Surf. Sci., 2006, 252, 4289–4297 CrossRef CAS.
- M. A. Cauqui and J. M. Rodríguez-Izquierdo, J. Non-Cryst. Solids, 1992, 147–148, 724–738 CrossRef CAS.
- S. S. Kistler, Nature, 1931, 127, 741 CrossRef CAS.
- S. D. Bhagat, Y.-H. Kim, K.-H. Suh, Y.-S. Ahn, J.-G. Yeo and J.-H. Han, Microporous Mesoporous Mater., 2008, 112, 504–509 CrossRef CAS.
- Y. Si, J. Yu, X. Tang, J. Ge and B. Ding, Nat. Commun., 2014, 5, 5802 CrossRef PubMed.
- C. Jia, L. Li, Y. Liu, B. Fang, H. Ding, J. Song, Y. Liu, K. Xiang, S. Lin, Z. Li, W. Si, B. Li, X. Sheng, D. Wang, X. Wei and H. Wu, Nat. Commun., 2020, 11, 3732 CrossRef CAS PubMed.
- L. Su, H. Wang, M. Niu, S. Dai, Z. Cai, B. Yang, H. Huyan and X. Pan, Sci. Adv., 2020, 6, eaay6689 CrossRef CAS PubMed.
- J. Yang, H. Wang, B. Zhou, J. Shen, Z. Zhang and A. Du, Langmuir, 2021, 37, 2129–2139 CrossRef CAS PubMed.
- S. Zhao, G. Siqueira, S. D Rdova, D. Norris and W. J. Malfait, Nature, 2020, 584, 387–392 CrossRef CAS PubMed.
- N. Karamat-Ullah, Y. Demidov, M. Schramm, D. Grumme, J. Auer, C. Bohr, B. Brachvogel and H. Maleki, ACS Biomater. Sci. Eng., 2021, 7, 4545–4556 CrossRef CAS PubMed.
- J. J. Moyano, J. Loizillon, D. Pérez-Coll, M. Belmonte, P. Miranzo, D. Grosso and M. I. Osendi, J. Eur. Ceram. Soc., 2021, 41, 2908–2917 CrossRef CAS.
- A. Du, H. Wang, B. Zhou, C. Zhang, X. Wu, Y. Ge, T. Niu, X. Ji, T. Zhang, Z. Zhang, G. Wu and J. Shen, Chem. Mater., 2018, 30, 6849–6857 CrossRef CAS.
- P. Hu, L. Liu, M. Zhao, J. Wang, X. Ma and J. Wang, ES Mater. Manuf., 2021, 15, 14–33 Search PubMed.
- T. Huang, Y. Zhu, J. Zhu, H. Yu, Q. Zhang and M. Zhu, Adv. Fiber Mater., 2020, 2, 338–347 CrossRef CAS.
- P. B. Sarawade, J.-K. Kim, A. Hilonga and H. T. Kim, Solid State Sci., 2010, 12, 911–918 CrossRef CAS.
- S. Yun, T. Guo, J. Zhang, L. He, Y. Li, H. Li, X. Zhu and Y. Gao, J. Sol-Gel Sci. Technol., 2017, 83, 53–63 CrossRef CAS.
- T.-Y. Wei, T.-F. Chang, S.-Y. Lu and Y.-C. Chang, J. Am. Ceram. Soc., 2007, 90, 2003–2007 CrossRef CAS.
- P. Tsou, J. Non-Cryst. Solids, 1995, 186, 415–427 CrossRef CAS.
- J. Matijevic and D. Shirley, Control Eng. Pract., 1997, 5, 827–835 CrossRef.
- M. Tabata, I. Adachi, H. Kawai, M. Kubo and T. Sato, Phys. Procedia, 2012, 37, 642–649 CrossRef CAS.
- M. Reim, A. Beck, W. Körner, R. Petricevic, M. Glora, M. Weth, T. Schliermann, J. Fricke, C. Schmidt and F. J. Pötter, Sol. Energy, 2002, 72, 21–29 CrossRef CAS.
- J. Wernery, A. Ben-Ishai, B. Binder and S. Brunner, Energy Procedia, 2017, 134, 490–498 CrossRef CAS.
- H. Liu, W. Sha, A. T. Cooper and M. Fan, Colloids Surf., A, 2009, 347, 38–44 CrossRef CAS.
- T. Liu, Q. Liu, Y. Liu, H. Yao, Z. Zhang, X. Wang and J. Shen, J. Sol-Gel Sci. Technol., 2021, 98, 389–400 CrossRef CAS.
- S. Štandeker, Z. Novak and Ž. Knez, J. Colloid Interface Sci., 2007, 310, 362–368 CrossRef PubMed.
- Y. Yu, Q. Ma, J.-b. Zhang and G.-b. Liu, Appl. Surf. Sci., 2020, 512, 145697 CrossRef CAS.
- Y. Song, X. Chen, T. Hao, Z. Liu and Z. Lan, Comput. Educ., 2019, 137, 12–31 CrossRef.
- O. Ellegaard and J. A. Wallin, Scientometrics, 2015, 105, 1809–1831 CrossRef PubMed.
- S. Zhu, H. Meng, Z. Gu and Y. Zhao, Nano Today, 2021, 39, 101233 CrossRef.
- S. Zhu, L. Li, Z. Gu, C. Chen and Y. Zhao, Small, 2020, 16, 2000980 CrossRef CAS PubMed.
- J. Xie, M. Zhao, C. Wang, Y. Yong and Z. Gu, Chem. Eng. J., 2022, 435, 134976 CrossRef CAS.
- K. Ullmann, P. Ádám and K. Sinkó, J. Non-Cryst. Solids, 2018, 499, 394–400 CrossRef CAS.
- C. Macías, M. Haro, J. B. Parra, G. Rasines and C. O. Ania, Carbon, 2013, 63, 487–497 CrossRef.
- Z. Zahedi and S. Haustein, J. Informetr, 2018, 12, 191–202 CrossRef.
- K. Saikia, M. Vallès, A. Fabregat, R. Saez and D. Boer, Sol. Energy, 2020, 199, 100–114 CrossRef.
- J. Tse, D. E. Schrader, D. Ghosh, T. Liao and D. Lundie, Ethics Inf. Technol., 2015, 17, 153–163 CrossRef.
- P. Ball, Nature, 2005, 436, 900 CrossRef CAS PubMed.
- A. Thor and L. Bornmann, Online Inf. Rev., 2011, 35, 291–300 CrossRef.
- L. Ding, L. Chen, C. Ding and J. Tao, Chin. Geogr. Sci., 2019, 29, 1–12 CrossRef.
- N. van Eck and L. Waltman, Scientometrics, 2010, 84, 523–538 CrossRef PubMed.
- P. B. Wagh, R. Begag, G. M. Pajonk, A. V. Rao and D. Haranath, Mater. Chem. Phys., 1999, 57, 214–218 CrossRef CAS.
- L. Wang, J. Feng, Y. Luo, Z. Zhou, Y. Jiang, X. Luo, L. Xu, L. Li and J. Feng, ACS Appl. Mater. Interfaces, 2021, 13, 40964–40975 CrossRef PubMed.
- J. L. Gurav, I.-K. Jung, H.-H. Park, E. S. Kang and D. Y. Nadargi, J. Nanomater., 2010, 2010, 409310 Search PubMed.
- Q. Liu, K. Yan, J. Chen, M. Xia, M. Li, K. Liu, D. Wang, C. Wu and Y. Xie, Aggregate, 2021, 2, e30 Search PubMed.
- Z. Guo, R. Yang, T. Wang, L. An, S. Ren and C. Zhou, J. Manuf. Sci. Eng., 2020, 143, 011011 CrossRef.
- G. Guzel Kaya and H. Deveci, J. Ind. Eng. Chem., 2020, 89, 13–27 CrossRef CAS.
- L. L. Hench and J. K. West, Chem. Rev., 1990, 90, 33–72 CrossRef CAS.
- H. Tamon, T. Kitamura and M. Okazaki, J. Colloid Interface Sci., 1998, 197, 353–359 CrossRef CAS PubMed.
- H. Maleki, L. Durães and A. Portugal, J. Non-Cryst. Solids, 2014, 385, 55–74 CrossRef CAS.
- Z. Shao, F. Luo, X. Cheng and Y. Zhang, Mater. Chem. Phys., 2013, 141, 570–575 CrossRef CAS.
- C. J. Lee, G. S. Kim and S. H. Hyun, J. Mater. Sci., 2002, 37, 2237–2241 CrossRef CAS.
- D. Y. Nadargi and A. V. Rao, J. Alloys Compd., 2009, 467, 397–404 CrossRef CAS.
- A. Venkateswara Rao, S. D. Bhagat, H. Hirashima and G. M. Pajonk, J. Colloid Interface Sci., 2006, 300, 279–285 CrossRef PubMed.
- Z. Yang, H. Yu, X. Li, H. Ding and H. Ji, J. Non-Cryst. Solids, 2019, 525, 119677 CrossRef CAS.
- K.-Y. Lee, D. B. Mahadik, V. G. Parale and H.-H. Park, J. Korean Ceram. Soc., 2019, 57, 1–23 Search PubMed.
- K. Sinkó, Materials, 2010, 3, 704–740 CrossRef.
- A. Venkateswara Rao, G. M. Pajonk and N. N. Parvathy, J. Mater. Sci., 1994, 29, 1807–1817 CrossRef.
- C. J. Brinker, J. Non-Cryst. Solids, 1988, 100, 31–50 CrossRef CAS.
- R. Ciriminna, A. Fidalgo, V. Pandarus, F. Béland, L. M. Ilharco and M. Pagliaro, Chem. Rev., 2013, 113, 6592–6620 CrossRef CAS PubMed.
- K. Nawaz, S. J. Schmidt and A. M. Jacobi, Int. J. Heat Mass Transfer, 2014, 74, 25–34 CrossRef CAS.
- A. Buckley and M. Greenblatt, J. Chem. Educ., 1994, 71, 599 CrossRef CAS.
- D. Y. Nadargi, S. S. Latthe and A. Venkateswara Rao, J. Sol-Gel Sci. Technol., 2009, 49, 53–59 CrossRef CAS.
- R. A. Strøm, Y. Masmoudi, A. Rigacci, G. Petermann, L. Gullberg, B. Chevalier and M. A. Einarsrud, J. Sol-Gel Sci. Technol., 2007, 41, 291–298 CrossRef.
- S. Smitha, P. Shajesh, P. R. Aravind, S. R. Kumar, P. K. Pillai and K. G. K. Warrier, Microporous Mesoporous Mater., 2006, 91, 286–292 CrossRef CAS.
- S. Hæreid, M. Dahle, S. Lima and M. A. Einarsrud, J. Non-Cryst. Solids, 1995, 186, 96–103 CrossRef.
- M.-A. Einarsrud, M. Britt Kirkedelen, E. Nilsen, K. Mortensen and J. Samseth, J. Non-Cryst. Solids, 1998, 231, 10–16 CrossRef CAS.
- H. Omranpour, A. Dourbash and S. Motahari, AIP Conf. Proc., 2014, 1593, 298–302 CrossRef CAS.
- H. Omranpour and S. Motahari, J. Non-Cryst. Solids, 2013, 379, 7–11 CrossRef CAS.
- A. Pons, L. Casas, E. Estop, E. Molins, K. D. M. Harris and M. Xu, J. Non-Cryst. Solids, 2012, 358, 461–469 CrossRef CAS.
- W. P. Lee and A. F. Routh, Langmuir, 2004, 20, 9885–9888 CrossRef CAS PubMed.
- S. He, D. Huang, H. Bi, Z. Li, H. Yang and X. Cheng, J. Non-Cryst.
Solids, 2015, 410, 58–64 CrossRef CAS.
- H. Maleki, L. Durães and A. Portugal, J. Phys. Chem. C, 2015, 119, 7689–7703 CrossRef CAS.
- S. S. Çok and N. Gizli, Ceram. Int., 2020, 46, 27789–27799 CrossRef.
- S.-W. Liu, Q. Wei, S.-P. Cui, Z.-R. Nie, M.-H. Du and Q.-Y. Li, J. Sol-Gel Sci. Technol., 2016, 78, 60–67 CrossRef CAS.
- M. V. Khedkar, S. B. Somvanshi, A. V. Humbe and K. M. Jadhav, J. Non-Cryst. Solids, 2019, 511, 140–146 CrossRef CAS.
- T. Li, A. Du, T. Zhang, W. Ding, M. Liu, J. Shen, Z. Zhang and B. Zhou, RSC Adv., 2018, 8, 17967–17975 RSC.
- D. Sivaraman, S. Zhao, S. Iswar, M. Lattuada and W. J. Malfait, Adv. Eng. Mater., 2021, 23, 2100376 CrossRef CAS.
- A. Venkateswara Rao, A. Parvathy Rao and M. M. Kulkarni, J. Non-Cryst. Solids, 2004, 350, 224–229 CrossRef.
- C. Ratti, J. Food Eng., 2001, 49, 311–319 CrossRef.
- W. Abdelwahed, G. Degobert, S. Stainmesse and H. Fessi, Adv. Drug Delivery Rev., 2006, 58, 1688–1713 CrossRef CAS PubMed.
- C. Gallé, Cem. Concr. Res., 2001, 31, 1467–1477 CrossRef.
- G. W. Scherer, J. Non-Cryst. Solids, 1993, 155, 1–25 CrossRef CAS.
- L. T. Canham, A. G. Cullis, C. Pickering, O. D. Dosser, T. I. Cox and T. P. Lynch, Nature, 1994, 368, 133–135 CrossRef CAS.
- Z. Zhang and G. W. Scherer, Cem. Concr. Res., 2017, 99, 137–154 CrossRef CAS.
- G. Guzel Kaya, E. Yilmaz and H. Deveci, Adv. Powder Technol., 2020, 31, 926–936 CrossRef CAS.
- Q. Fu, Y. Si, C. Duan, Z. Yan, L. Liu, J. Yu and B. Ding, Adv. Funct. Mater., 2019, 29, 1808234 CrossRef.
- M. Dilamian, M. Joghataei, Z. Ashrafi, C. Bohr, S. Mathur and H. Maleki, Appl. Mater. Today, 2021, 22, 100964 CrossRef.
- T. Pirzada, Z. Ashrafi, W. Xie and S. A. Khan, Adv. Funct. Mater., 2020, 30, 1907359 CrossRef CAS.
- C. Ferraro, E. Garcia-Tuñon, V. G. Rocha, S. Barg, M. D. Fariñas, T. E. G. Alvarez-Arenas, G. Sernicola, F. Giuliani and E. Saiz, Adv. Funct. Mater., 2016, 26, 1636–1645 CrossRef CAS.
- G. Shao, D. A. H. Hanaor, X. Shen and A. Gurlo, Adv. Mater., 2020, 32, 1907176 CrossRef CAS PubMed.
- S. A. Barr and E. Luijten, Acta Mater., 2010, 58, 709–715 CrossRef CAS.
- S. Deville, Adv. Eng. Mater., 2008, 10, 155–169 CrossRef CAS.
- N. Arai, T. Stan, S. Macfarland, P. W. Voorhees, N. S. Muyanja, A. J. Shahani and K. T. Faber, Acta Mater., 2021, 215, 117039 CrossRef CAS.
- M. C. Gutiérrez, Z. Y. García-Carvajal, M. Jobbágy, F. Rubio, L. Yuste, F. Rojo, M. L. Ferrer and F. del Monte, Adv. Funct. Mater., 2007, 17, 3505–3513 CrossRef.
- K. H. Zuo, Y.-P. Zeng and D. Jiang, Mater. Sci. Eng., C, 2010, 30, 283–287 CrossRef CAS PubMed.
- C. M. Pekor, P. Kisa and I. Nettleship, J. Am. Ceram. Soc., 2008, 91, 3185–3190 CrossRef CAS.
- X. Li, D. Yao, K. Zuo, Y. Xia, J. Yin, H. Liang and Y.-P. Zeng, J. Eur. Ceram. Soc., 2020, 40, 5845–5851 CrossRef CAS.
- L. Xian, Y. Zhang, Y. Wu, X. Zhang, X. Dong, J. Liu and A. Guo, Ceram. Int., 2020, 46, 1869–1875 CrossRef CAS.
- M. Sun, S. Yang, X. Gao, P. Man, J. Qu, W. Zhang, S. Yin and L. Cheng, Ceram. Int., 2021, 47, 8169–8174 CrossRef CAS.
- J. Halloran, Science, 2006, 311, 479–480 CrossRef CAS PubMed.
- M.-A. Shahbazi, M. Ghalkhani and H. Maleki, Adv. Eng. Mater., 2020, 22, 2000033 CrossRef CAS.
- S. Deville, E. Saiz and A. P. Tomsia, Biomaterials, 2006, 27, 5480–5489 CrossRef CAS PubMed.
- K. Araki and J. W. Halloran, J. Am. Ceram. Soc., 2004, 87, 2014–2019 CrossRef CAS.
- Y. Si, X. Wang, L. Dou, J. Yu and B. Ding, Sci. Adv., 2018, 4, eaas8925 CrossRef PubMed.
- F. Wang, L. Dou, J. Dai, Y. Li, L. Huang, Y. Si, J. Yu and B. Ding, Angew. Chem., Int. Ed., 2020, 59, 8285–8292 CrossRef CAS PubMed.
- L. Qiu, J. Z. Liu, S. L. Y. Chang, Y. Wu and D. Li, Nat. Commun., 2012, 3, 1241 CrossRef PubMed.
- D. J. Sypeck and H. N. G. Wadley, Adv. Eng. Mater., 2002, 4, 759–764 CrossRef CAS.
- L. Dou, X. Zhang, X. Cheng, Z. Ma, X. Wang, Y. Si, J. Yu and B. Ding, ACS Appl. Mater. Interfaces, 2019, 11, 29056–29064 CrossRef CAS PubMed.
- X. Xu, Q. Zhang, M. Hao, Y. Hu, Z. Lin, L. Peng, T. Wang, X. Ren, C. Wang, Z. Zhao, C. Wan, H. Fei, L. Wang, J. Zhu, H. Sun, W. Chen, T. Du, B. Deng, J. Cheng Gary, I. Shakir, C. Dames, S. Fisher Timothy, X. Zhang, H. Li, Y. Huang and X. Duan, Science, 2019, 363, 723–727 CrossRef CAS PubMed.
- T. M. Tillotson and L. W. Hrubesh, J. Non-Cryst. Solids, 1992, 145, 44–50 CrossRef CAS.
- H. Wang, X. Zhang, N. Wang, Y. Li, X. Feng, Y. Huang, C. Zhao, Z. Liu, M. Fang, G. Ou, H. Gao, X. Li and H. Wu, Sci. Adv., 2017, 3, e1603170 CrossRef PubMed.
- T. Tian, T.-W. Zhang, Y.-C. Yin, Y.-H. Tan, Y.-H. Song, L.-L. Lu and H.-B. Yao, Nano Lett., 2019, 20, 677–685 CrossRef PubMed.
- J. A. Lewis, Adv. Funct. Mater., 2006, 16, 2193–2204 CrossRef CAS.
- V. C.-F. Li, C. K. Dunn, Z. Zhang, Y. Deng and H. J. Qi, Sci. Rep., 2017, 7, 8018 CrossRef PubMed.
- Z. Guo, R. Yang, T. Wang, L. An, S. Ren and C. Zhou, J. Manuf. Sci. Eng., 2021, 143, 011011 CrossRef.
- B. S. Chava, E. K. Thorn and S. Das, Phys. Chem. Chem. Phys., 2021, 23, 24634–24645 RSC.
- A. Shahzad and I. Lazoglu, Composites, Part B, 2021, 225, 109249 CrossRef CAS.
- D. Kam, M. Chasnitsky, C. Nowogrodski, I. Braslavsky, T. Abitbol, S. Magdassi and O. Shoseyov, Colloids Interfaces, 2019, 3, 46 CrossRef CAS.
- H. Tetik, Y. Wang, X. Sun, D. Cao, N. Shah, H. Zhu, F. Qian and D. Lin, Adv. Funct. Mater., 2021, 31, 2103410 CrossRef CAS.
- J. Ma, F. Ye, C. Yang, J. Ding, S. Lin, B. Zhang and Q. Liu, Mater. Des., 2017, 131, 226–231 CrossRef CAS.
- N. Leventis, C. Sotiriou-Leventis, G. Zhang and A.-M. M. Rawashdeh, Nano Lett., 2002, 2, 957–960 CrossRef CAS.
- R. Liu, X. Dong, S. Xie, T. Jia, Y. Xue, J. Liu, W. Jing and A. Guo, Chem. Eng. J., 2019, 360, 464–472 CrossRef CAS.
- S. Karamikamkar, H. E. Naguib and C. B. Park, Adv. Colloid Interface Sci., 2020, 276, 102101 CrossRef CAS PubMed.
- L. Jiang, K. Kato, K. Mayumi, H. Yokoyama and K. Ito, ACS Macro Lett., 2017, 6, 281–286 CrossRef CAS.
- M. A. B. Meador, E. F. Fabrizio, F. Ilhan, A. Dass, G. Zhang, P. Vassilaras, J. C. Johnston and N. Leventis, Chem. Mater., 2005, 17, 1085–1098 CrossRef CAS.
- S. P. Patil, P. Shendye and B. Markert, Composites, Part B, 2020, 190, 107884 CrossRef CAS.
- A. Lamy-Mendes, W. J. Malfait, A. Sadeghpour, A. V. Girão, R. F. Silva and L. Durães, Carbon, 2021, 180, 146–162 CrossRef CAS.
- A. Ślosarczyk, Nanomaterials, 2017, 7, 44 CrossRef PubMed.
- J. He, H. Zhao, X. Li, D. Su, F. Zhang, H. Ji and R. Liu, J. Hazard. Mater., 2018, 346, 199–207 CrossRef CAS PubMed.
- G. Wei, Y. Liu, X. Zhang, F. Yu and X. Du, Int. J. Heat Mass Transfer, 2011, 54, 2355–2366 CrossRef CAS.
- J. Fricke, X. Lu, P. Wang, D. Büttner and U. Heinemann, Int. J. Heat Mass Transfer, 1992, 35, 2305–2309 CrossRef CAS.
- J. Fricke and T. Tillotson, Thin Solid Films, 1997, 297, 212–223 CrossRef CAS.
- N. Bheekhun, A. R. Abu Talib and M. R. Hassan, Adv. Mater. Sci. Eng., 2013, 2013, 1–18 CrossRef.
- V. P. Carey, G. Chen, C. Grigoropoulos, M. Kaviany and A. Majumdar, Nanoscale Microscale Thermophys. Eng., 2008, 12, 1–60 CrossRef CAS.
- D. Bi, H. Chen and T. Ye, Cryogenics, 2012, 52, 403–409 CrossRef CAS.
- A. J. H. McGaughey and M. Kaviany, Int. J. Heat Mass Transfer, 2004, 47, 1799–1816 CrossRef CAS.
- R. Prasher, Nano Lett., 2005, 5, 2155–2159 CrossRef CAS PubMed.
- Y. Lei, Z. Hu, B. Cao, X. Chen and H. Song, Mater. Chem. Phys., 2017, 187, 183–190 CrossRef CAS.
- Z. Deng, J. Wang, A. Wu, J. Shen and B. Zhou, J. Non-Cryst. Solids, 1998, 225, 101–104 CrossRef CAS.
- V. Apostolopoulou-Kalkavoura, P. Munier and L. Bergström, Adv. Mater., 2021, 33, 2001839 CrossRef CAS PubMed.
- Y. Lei, X. Chen, Z. Hu, H. Song and B. Cao, Scr. Mater., 2017, 139, 5–8 CrossRef CAS.
- L. Dou, X. Cheng, X. Zhang, Y. Si, J. Yu and B. Ding, J. Mater. Chem. A, 2020, 8, 7775–7783 RSC.
- S. Liu, X. Wu, Y. Li, S. Cui, X. Shen and G. Tan, Appl. Therm. Eng., 2021, 190, 116745 CrossRef CAS.
- L. Shang, Y. Lyu and W. Han, Materials, 2019, 12, 993 CrossRef CAS PubMed.
- H. Zhang, W.-Z. Fang, X. Wang, Y.-M. Li and W.-Q. Tao, Int. J. Heat Mass Transfer, 2017, 115, 21–31 CrossRef CAS.
- J. Zhu, H. Ren and Y. Bi, J. Porous Mater., 2018, 25, 1697–1705 CrossRef CAS.
- V. G. Parale, H.-N.-R. Jung, W. Han, K.-Y. Lee, D. B. Mahadik, H. H. Cho and H.-H. Park, J. Alloys Compd., 2017, 727, 871–878 CrossRef CAS.
- K. Rehman, F. Fatima, I. Waheed and M. S. H. Akash, J. Cell. Biochem., 2018, 119, 157–184 CrossRef CAS PubMed.
- S. Štandeker, Z. Novak and Ž. Knez, J. Hazard. Mater., 2009, 165, 1114–1118 CrossRef PubMed.
- M.-H. Sun, S.-Z. Huang, L.-H. Chen, Y. Li, X.-Y. Yang, Z.-Y. Yuan and B.-L. Su, Chem. Soc. Rev., 2016, 45, 3479–3563 RSC.
- N. Hüsing and U. Schubert, J. Sol-Gel Sci. Technol., 1997, 8, 807–812 Search PubMed.
- H. R. Pouretedal and M. Kazemi, Int. J. Ind. Chem., 2012, 3, 20 CrossRef.
- F. Tadayon, M. Saber-Tehrani and S. Motahar, Korean J. Chem. Eng., 2013, 30, 642–648 CrossRef CAS.
- H. Faghihian, H. Nourmoradi and M. Shokouhi, Desalin. Water Treat., 2013, 52, 305–313 CrossRef.
- S. Štandeker, A. Veronovski, Z. Novak and Ž. Knez, Desalination, 2011, 269, 223–230 CrossRef.
- T. Fariba, H. Mina and M. Shiva, J. Chin. Chem. Soc., 2012, 59, 1578–1583 CrossRef.
- Z. Shariatinia and A. Esmaeilzadeh, Water Environ. Res., 2019, 91, 1624–1637 CrossRef CAS PubMed.
- P. Herman, I. Fábián and J. Kalmár, ACS Appl. Nano Mater., 2020, 3, 195–206 CrossRef CAS.
- P. K. Jal, S. Patel and B. K. Mishra, Talanta, 2004, 62, 1005–1028 CrossRef CAS PubMed.
- M. Hasanpour and M. Hatami, Adv. Colloid Interface Sci., 2020, 284, 102247 CrossRef CAS PubMed.
- H. Maleki, Chem. Eng. J., 2016, 300, 98–118 CrossRef CAS.
- S. S. Mirzaee, E. Salahi and A. Khanlarkhani, J. Dispersion Sci. Technol., 2019, 40, 657–667 CrossRef CAS.
- M. Li, M.-y. Li, C.-g. Feng and Q.-x. Zeng, Appl. Surf. Sci., 2014, 314, 1063–1069 CrossRef CAS.
- S. Sertsing, T. Chukeaw, S. Pengpanich and B. Pornchuti, MATEC Web Conf., 2018, 156, 03014 CrossRef.
- L. Zhang, C. Yu, W. Zhao, Z. Hua, H. Chen, L. Li and J. Shi, J. Non-Cryst. Solids, 2007, 353, 4055–4061 CrossRef CAS.
- C. M. C. Filho, T. Matias, L. Durães and A. J. M. Valente, Colloids Surf., A, 2017, 520, 550–560 CrossRef CAS.
- R. Tang, W. Hong, C. Srinivasakannan, X. Liu, X. Wang and X. Duan, Sep. Purif. Technol., 2022, 281, 119950 CrossRef CAS.
- J. Huang, H. Liu, S. Chen and C. Ding, J. Environ. Chem. Eng., 2016, 4, 3274–3282 CrossRef CAS.
- D. D. E. Koyuncu and M. Okur, Colloids Surf., A, 2021, 628, 127370 CrossRef CAS.
- A. Abolghasemi Mahani, S. Motahari and A. Mohebbi, Mar. Pollut. Bull., 2018, 129, 438–447 CrossRef CAS PubMed.
- K. Chen, Q. Feng, D. Ma and X. Huang, Colloids Surf., A, 2021, 616, 126331 CrossRef CAS.
- Y. Kong, X. Shen, S. Cui and M. Fan, Appl. Energy, 2015, 147, 308–317 CrossRef CAS.
- S. Sert Çok, F. Koç and N. G
zl
, J. Hazard. Mater., 2021, 408, 124858 CrossRef PubMed. - C. Chen, S. Zhang, K. H. Row and W.-S. Ahn, J. Energy Chem., 2017, 26, 868–880 CrossRef CAS.
- N. N. Linneen, R. Pfeffer and Y. S. Lin, Chem. Eng. J., 2014, 254, 190–197 CrossRef CAS.
- P. Zhao, G. Zhang, Y. Xu, Y.-K. Lv, Z. Yang and H. Cheng, Energy Fuels, 2019, 33, 3357–3369 CrossRef CAS.
- Y. Guo, C. Zhao, J. Sun, W. Li and P. Lu, Fuel, 2018, 215, 735–743 CrossRef CAS.
- T. M. Shaffer, E. C. Pratt and J. Grimm, Nat. Nanotechnol., 2017, 12, 106–117 CrossRef CAS PubMed.
- C. Lippmann, Nucl. Instrum. Methods Phys. Res., Sect. A, 2012, 666, 148–172 CrossRef CAS.
- L. Cremaldi, D. A. Sanders, P. Sonnek, D. J. Summers and J. Reidy, IEEE Trans. Nucl. Sci., 2009, 56, 1475–1478 Search PubMed.
- Y. N. Kharzheev, Phys. Part. Nucl., 2008, 39, 107–135 CrossRef CAS.
- C. Grupen, AIP Conf. Proc., 2000, 536, 3–34 CrossRef CAS.
- J. Seguinot and T. Ypsilantis, Nucl. Instrum. Methods Phys. Res., Sect. A, 1994, 343, 1–29 CrossRef CAS.
- I. Adachi, T. Sumiyoshi, K. Hayashi, N. Iida, R. Enomoto, K. Tsukada, R. Suda, S. Matsumoto, K. Natori, M. Yokoyama and H. Yokogawa, Nucl. Instrum. Methods Phys. Res., Sect. A, 1995, 355, 390–398 CrossRef CAS.
- T. Bellunato, A. Braem, A. R. Buzykaev, M. Calvi, E. Chesi, A. F. Danilyuk, S. Easo, C. Hansen, S. Jolly, C. Joram, E. A. Kravchenko, D. Liko, C. Matteuzzi, M. Musy, P. Negri, N. Neufeld, A. P. Onuchin, J. Seguinot, P. Weilhammer and S. Wotton, Nucl. Instrum. Methods Phys. Res., Sect. A, 2003, 502, 227–230 CrossRef CAS.
- E. T. Hwang and M. B. Gu, Eng. Life Sci., 2013, 13, 49–61 CrossRef CAS.
- S. Paul and J. H. Clark, Green Chem., 2003, 5, 635–638 RSC.
- M. Paljevac, M. Primožič, M. Habulin, Z. Novak and Ž. Knez, J. Supercrit. Fluids, 2007, 43, 74–80 CrossRef CAS.
- A. Wolny and A. Chrobok, Nanomaterials, 2021, 11, 2030 CrossRef CAS PubMed.
- T. Jesionowski, J. Zdarta and B. Krajewska, Adsorption, 2014, 20, 801–821 CrossRef CAS.
- M. C. Lisboa, C. A. Rodrigues, A. S. Barbosa, S. Mattedi, L. S. Freitas, A. A. Mendes, C. Dariva, E. Franceschi, Á. Lima and C. M. F. Soares, Process Biochem., 2018, 75, 157–165 CrossRef CAS.
- P. Veres, M. Kéri, I. Bányai, I. Lázár, I. Fábián, C. Domingo and J. Kalmár, Colloids Surf., B, 2017, 152, 229–237 CrossRef CAS PubMed.
- J. Stergar and U. Maver, J. Sol-Gel Sci. Technol., 2016, 77, 738–752 CrossRef CAS.
- H. Maleki, L. Durães, C. A. García-González, P. del Gaudio, A. Portugal and M. Mahmoudi, Adv. Colloid Interface Sci., 2016, 236, 1–27 CrossRef CAS PubMed.
- N. Ganonyan, G. Bar, R. Gvishi and D. Avnir, RSC Adv, 2021, 11, 7824–7838 RSC.
- D. D. Lovskaya, A. E. Lebedev and N. V. Menshutina, J. Supercrit. Fluids, 2015, 106, 115–121 CrossRef CAS.
- I. Smirnova, S. Suttiruengwong, M. Seiler and W. Arlt, Pharm. Dev. Technol., 2005, 9, 443–452 CrossRef PubMed.
- L. W. Hrubesh, J. Non-Cryst. Solids, 1998, 225, 335–342 CrossRef CAS.
- L. Xiao, M. D. W. Grogan, W. J. Wadsworth, R. England and T. A. Birks, Opt. Express, 2011, 19, 764–769 CrossRef CAS PubMed.
- T. M. Tillotson, W. E. Sunderland, I. M. Thomas and L. W. Hrubesh, J. Sol-Gel Sci. Technol., 1994, 1, 241–249 CrossRef CAS.
- J. P. Nayak and J. Bera, Trans. Indian Ceram. Soc., 2009, 68, 91–94 CrossRef CAS.
- A. Tadjarodi, M. Haghverdi and V. Mohammadi, Mater. Res. Bull., 2012, 47, 2584–2589 CrossRef CAS.
- S. Ma, H. Yang, S. Zhao, P. He, Z. Zhang, X. Duan, Z. Yang, D. Jia and Y. Zhou, Composites, Part B, 2021, 226, 109348 CrossRef CAS.
Footnote |
† These authors contributed equally to this work. |
|
This journal is © The Royal Society of Chemistry 2022 |
Click here to see how this site uses Cookies. View our privacy policy here.