DOI:
10.1039/D3RA02352D
(Paper)
RSC Adv., 2023,
13, 17914-17922
Vertically aligned MoS2 nanosheets on monodisperse MXene as electrolyte-philic cathodes for zinc ion batteries with enhanced capacity†
Received
10th April 2023
, Accepted 29th May 2023
First published on 14th June 2023
Abstract
Zinc ion batteries (ZIBs) have attracted extensive attention for their high safety and environmentally friendly nature, and considerable theoretical capacities. Due to its unique two-dimensional layered structure and high theoretical specific capacities, molybdenum disulfide (MoS2) presents as a promising cathode material for ZIBs. Nevertheless, the low electrical conductivity and poor hydrophilicity of MoS2 limits its wide application in ZIBs. In this work, MoS2/Ti3C2Tx composites are effectively constructed using a one-step hydrothermal method, where two-dimensional MoS2 nanosheets are vertically grown on monodisperse Ti3C2Tx MXene layers. Contributing to the high ionic conductivity and good hydrophilicity of Ti3C2Tx, MoS2/Ti3C2Tx composites possess improved electrolyte-philic and conductive properties, leading to a reduced volume expansion effect of MoS2 and accelerated Zn2+ reaction kinetics. As a result, MoS2/Ti3C2Tx composites exhibit high voltage (1.6 V) and excellent discharge specific capacity of 277.8 mA h g−1 at 0.1 A g−1, as well as cycle stability as cathode materials for ZIBs. This work provides an effective strategy for developing cathode materials with high specific capacity and stable structure.
Introduction
In recent years, with the rapid development of the economy and increasing energy consumption, high-capacity batteries are highly desired for energy storage purposes.1–3 In these respects, lithium-ion batteries have been widely used in electronic products and transportation industries due to their high energy density.1,4,5 However, lithium-ion batteries suffer from the problems of high production cost and intrinsic safety issues. Extensive research has been conducted on metal ion batteries (such as Mg2+, Zn2+, Na+, etc.), which are abundant in resources and low cost.1,6–10 Aqueous zinc ion batteries (ZIBs) are considered to be ideal candidates over lithium-ion batteries due to their low redox potential (−0.763 V vs. standard hydrogen electrode (SHE)),6,11–13 high theoretical specific capacity (820 mA h g−1 and 5855 mA h cm−3),14,15 non-toxic properties6 and abundant Zn resources.7 A typical ZIB generally compose of Zn metal anode, electrolyte, and cathode electrode for accommodating Zn ions.16 Except for the most common anode material of zinc metal in ZIBs, battery capacities are more limited by cathodes than anodes. With regards to the cathode materials, extensively investigated active materials include manganese-based materials, vanadium-based materials, Prussian blue analogs, and organic electrode materials and so on.17–21 However, the electrochemical and physical properties of these active materials are still inadequate to achieve high-performance ZIBs.22 It is urgent to develop cathode materials for ZIBs with high specific capacity and stable structures for large-scale commercial applications.23,24
Molybdenum disulfide (MoS2), a representative transition metal dichalcogenide, possesses the two-dimensional (2D) layered structure similar to graphite.25–27 The MoS2 is considered as promising host material for ion intercalation due to the unique layered structure bonded by weak van der Waals' forces.2,28,29 These characteristics indicate that the layered materials MoS2 demonstrate extraordinary potential as electrode materials for ZIBs.30,31 However, the low intrinsic conductivity, poor structural stability, and severe self-stacking of MoS2 hinder its wide application of MoS2 in zinc storage materials.2 In addition, the larger hydrated ionic diameter of Zn2+ (approximately 0.86 nm) and strong electrostatic interactions with MoS2 result in sluggish reaction kinetics and difficultly reversible Zn2+ intercalation.15,32–34 To alleviate these problems, several modification methods have been proposed to improve the electrochemical performance of ZIBs using MoS2, including the introduction of sulfur defects,35 partial replacement of sulfur atoms by oxygen atoms,36 modulation of phases,33 and expansion of layer spacing.37 For instance, Wang preferentially inserted Zn ions into sulfur vacancies building defect engineered MoS2−x nanosheets.35 The ZIBs based on MoS2−x nanosheets exhibited discharge specific capacity of 138.6 mA h g−1 at 0.1 A g−1. In another work, molecular engineering in terms of structure defects manufacturing and O-doping on MoS2 was reported by Li to expand the interlayer spacing (from 6.2 to 9.6 Å).26 Therefore, the tailored MoS2–O cathode respectively displayed specific capacity of 261 mA h g−1 at 0.1 A g−1 with 102.4 mA h g−1 at 10 A g−1, indicating unprecedentedly high rate-capability. In addition, due to metallic 1 T MoS2 with better electronic conductivity comparable than 2H MoS2, vertically aligned 1 T phase MoS2 nanosheet array on carbon cloth were fabricated to improve capacities.33 As a result, the free-standing cathode exhibited excellent specific capacity of 198 mA h g−1 at current density of 0.1 A g−1. Most recently, MoS2/polyaniline (PANI) hybrid with inter-overlapped heterostructure was explored with expanded interlayer spacing as large as 1.03 nm of (002) plane in the MoS2/PANI hybrid.37 The MoS2/PANI hybrid delivered high reversible capacity of 106.5 mA h g−1 at a current density of 1.0 A g−1. Nonetheless, the conductivity, swelling effect and self-aggregation phenomenon still need to be further improved to obtain high capacity and stable cycling ZIBs.
Ti3C2Tx MXene, typical 2D transition metal carbonitride, exhibits excellent properties, such as abundant surface groups,38 tunable interlayer spacing,39 excellent electrical conductivity40 and good hydrophilicity.41 Ti3C2Tx MXene has been widely developed and investigated for energy storage. Herein, the MoS2/Ti3C2Tx composites were constructed through the 2D MoS2 nanosheets vertically aligned on 2D Ti3C2Tx MXene by a one-step hydrothermal method. The resulting 3D open network architecture of the MoS2/Ti3C2Tx composites increased the interfacial contact with the electrolyte and shortened the diffusion pathways for Zn2+. Due to the high electrical conductivity and hydrophilicity of monodisperse Ti3C2Tx MXene, the introducing of Ti3C2Tx suppressed self-stacking of MoS2 nanosheets, accelerated the migration rate of Zn2+ and enhanced the reaction kinetic rate. Impressively, the as-fabricated MoS2/Ti3C2Tx composites exhibited high voltage to 1.6 V, high discharge specific capacity of 277.8 mA h g−1 at 0.1 A g−1 and 80% capacity retention after 5000 cycles when the current density was 10.0 A g−1. In addition, the intercalation/deintercalation mechanism and kinetic diffusion process of Zn ion diffusion were demonstrated using ex situ X-ray diffraction (ex-XRD), X-ray photoelectron spectroscopy (XPS) and galvanostatic intermittent titration technique (GITT). This work presented new insights on the application of layered materials as high-performance cathodes for ZIBs.
Experimental
Synthesis of Ti3C2Tx MXene
As previously reported, Ti3C2Tx was obtained after selective etching of the Al layer from Ti3AlC2 feedstock.42,43 First, 3.2 g LiF was dissolved in 40 mL HCl (9 mol L−1), stirred for five minutes and then 2 g Ti3AlC2 was slowly added to the above solution and the mixed solution was stirred at 35 °C for 24 h. The obtained mixed solution was washed with deionized water by centrifugation to a supernatant with pH of approximately 6, and the precipitate was sonicated with an appropriate amount of deionized water under argon for 1 h. Finally, the Ti3C2Tx dispersion was centrifuged at 3500 rpm for 20 min to obtain Ti3C2Tx dispersion.
Synthesis of MoS2/Ti3C2Tx MXene composites
In brief, 0.3 mmol ammonium molybdate and 13.1 mmol thiourea were dissolved in 50 mL water, and then 10 mg Ti3C2Tx (5 mg mL−1) was added to the mixed solution, which was stirred for 15 min at room temperature and sonicated for 5 min. The mixed solution was transferred to Teflon stainless steel kettles and reacted at 200 °C for 24 h. The resulting product was then washed three times with deionized water and freeze-dried for two days. In contrast, MoS2 nanosheets were synthesized without the addition of Ti3C2Tx. All the materials were used directly for electrochemical experiments without further purification.
Characterization methods
XRD were obtained using a Rigaku D/Max B diffractometer with Cu-Kα radiation. The morphology and microstructure of the samples were observed by field emission scanning electron microscopy (SEM, HITACHI, S-4800) and transmission electron microscopy (TEM, JEOL JEM-2100), respectively. XPS were measured by using Thermo Scientific Nexsa system to analysis the chemical composition of the material surface. The atomic force microscope (AFM) tested the sheet thickness of Ti3C2Tx MXene using Bruker Dimension Icon. The specific surface area was tested with Tri Star II 3020 by Michael Corporation, USA. Raman spectroscopy were performed with a DXRZXi model (Thermo, USA).
Electrochemical characterizations
Electrochemical performance tests were performed in a CR2032 coin cell with MoS2/Ti3C2Tx as the cathode, 0.1 mm zinc foil as the anode, 21 mol L−1 lithium bis(trifluoromethane sulfonyl) imide salt (LiTFSI, Innochem, 98%) and 1 mol L−1 Zn(CF3SO3)2 (TCI, >98%) as the electrolyte, and a glass fiber filter membrane (Whatman, GF/D) as the septum. The MoS2/Ti3C2Tx cathode was prepared by first grinding the active material, carbon black, and polyvinylidene fluoride (PVDF, Kejing Co. Shenzhen) in a 7
:
2
:
1 ratio in a mortar and pestle for thirty minutes, then pouring the solid powder into a small glass vial and adding an appropriate amount of N-methylpyrrolidone (NMP, Aladdin, >99%) solvent and stirring for 6 h. Finally, the mixed slurry was evenly coated on the titanium foil substrate and dried under vacuum at 80 °C for 12 h. The dried poles were cut into Φ = 12 mm discs, and the average active substance loading of the prepared cathodes was 1.0–1.5 mg cm−2. The cell multiplicity performance, cycling performance and GITT tests were carried out with the LAND 2001A cell test system in the voltage range of 0–1.6 V. Cyclic voltammetry (CV), electrochemical impedance spectrogram (EIS), and galvanostatic charge/discharge (GCD) were tested using the same electrochemical workstation (CHI 760E, C&H Co., Shanghai, China), and the frequency range of EIS spectrogram was 10−2–105. The above tests were performed at room temperature.
Results and discussion
Synthesis and characterization of MoS2/Ti3C2Tx composites
The MoS2/Ti3C2Tx MXene composites were synthesized via hydro-thermal reaction of (NH4)6Mo7O24·4H2O and NH2CSNH2 in presence of Ti3C2Tx MXene as illustrated in Fig. 1a. Prior to the hydro-thermal reaction, homogeneous single-layer Ti3C2Tx MXene dispersions with thickness of 2.2 nm (Fig. S1 and S2a†) were obtained through LiF and HCl etching of Ti3AlC2 MAX (Fig. S2b†), followed by ultrasonic process. The Raman spectra (Fig. 1b) and XRD patterns (Fig. S3–S4†) were recorded to understand the characteristic of MoS2/Ti3C2Tx MXene composites. According to the XRD pattern, the characteristic peaks of the (002) plane at 2θ values of 9.6° for Ti3AlC2 MAX shifted to 7.2° for Ti3C2Tx MXene, which was remarkedly shifted to 10.0° of MoS2/Ti3C2Tx MXene (Fig. S3†). In comparison to pure MoS2, the diffraction peak at the (002) plane of MoS2/Ti3C2Tx MXene was slightly shifted from 13.6° to 12.6°. Based on the Bragg's equation (nλ = 2d
sin
θ), the interlayer spacing of MoS2 was modified 0.65 nm of pure MoS2 from to 0.70 nm in the MoS2/Ti3C2Tx MXene composites. Furthermore, the characteristic peaks at 143.1 cm−1 (J1), 232.6 cm−1 (J2), and 332.5 cm−1 (J3) demonstrated the successful construction of dominating 1T MoS2 in heterostructure MoS2/Ti3C2Tx MXene (Fig. 1b). The peak located at 278.2 cm−1 was assigned to the E1g characteristic vibration of Mo in octahedral coordination, where the surface metal Mo atoms were connected to S atoms.
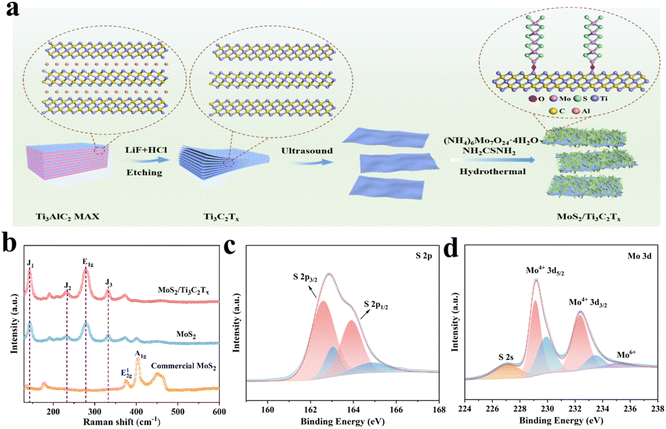 |
| Fig. 1 (a) Schematic synthesis of the MoS2/Ti3C2Tx composites. (b) Raman spectra of commercial MoS2, pure MoS2 and MoS2/Ti3C2Tx composites. Detailed XPS spectra of (c) S 2p and (d) Mo 3d. | |
The chemical composition and valence states of MoS2/Ti3C2Tx MXene composite were further analyzed using XPS spectra. The presence of Mo, S, Ti, C and O elements were confirmed in MoS2/Ti3C2Tx MXene composites (Fig. S5a†). In Ti 2p spectrum (Fig. S5b†), the signals at 458.3 and 463.7 eV were identified as the 2p3/2 and 2p1/2 orbits of Ti3+ in Ti3C2Tx MXene, respectively. The absence of 2p3/2 and 2p1/2 doublet at 458.7 and 464.6 eV indicated the absence of the Ti–O bonds in Ti3C2Tx MXene and surface-attached oxygen containing groups. Deposited in high-resolution S 2p spectrum (Fig. 1c), the S 2p3/2 and S 2p1/2 spectra were also deconvoluted into 1T and 2H phases. The peaks at binding energies of 162.6 eV and 163.9 eV were severally assigned to S 2p1/2 and S 2p3/2 of 1T phases, indicating the presence of divalent sulfur ions. The Mo6+ 3d3/2, Mo4+ 3d3/2 and Mo4+ 3d5/2 of 1T phases were characterized at 236.5 eV, 232.3 eV and 229.2 eV, respectively (Fig. 1d). The Mo in hierarchical structure of MoS2/Ti3C2Tx MXene composites were dominant in Mo4+ and minimal in the oxidization of Mo6+. Furthermore, different from the commercial MoS2 dominant in 2H phases (Fig. S6†), the MoS2/Ti3C2Tx MXene composites mainly consisted of 1T phase (about 66%), which was consistent with Raman spectra (Fig. 1b).
The morphology and structure of MoS2/Ti3C2Tx MXene composites were characterized using Scanning Electron Microscope (SEM), Energy Dispersive X-ray Spectroscopy (EDX) and Transmission Electron Microscope (TEM). The MoS2/Ti3C2Tx MXene composites exhibited flower-like structures with evident wrinkles and corrugations (Fig. 2a–c). Due to the existence of Ti3C2Tx MXene skeleton, heterogeneous nucleation avoided the agglomeration of MoS2 nanosheets. Moreover, MoS2 nanosheets were vertically aligned on the Ti3C2Tx MXene surface, displaying uniform distribution of C, Mo, S and Ti elements (Fig. 2d). The hierarchical structure of MoS2 nanosheets on the highly conductive Ti3C2Tx MXene substrate facilitated fast electron transfer and easy penetration of the electrolyte, resulting in considerable electrochemical properties. Furthermore, the staggered MoS2 nanosheets with low stacking height, providing lowered the Zn2+ migration potential barrier, provided more active sites for the intercalation of zinc ions.44 As elucidated in Fig. 2e–g, the fabricated MoS2 nanosheets exhibited the slightly modified interlayer spacing of 0.7 nm compared to commercial 2H MoS2 (0.65 nm, Fig. S7†), which was well in accordance with XRD data (Fig. 1b). Due to the reduced ion diffusion resistance and energy barrier, the enlarged interlayer spacing accelerated the reaction kinetics of Zn2+ for MoS2/Ti3C2Tx MXene composites.
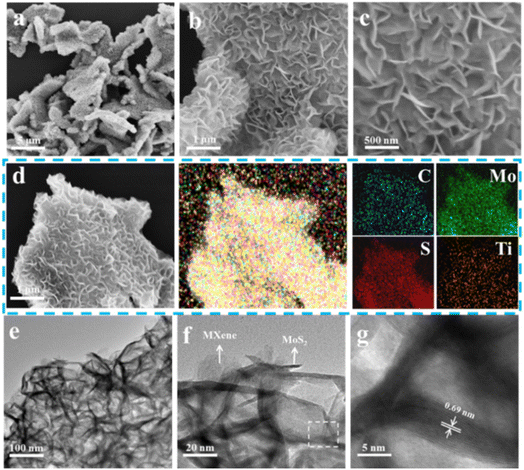 |
| Fig. 2 (a–c) SEM images, (d) element mapping and (e–g) TEM images of MoS2/Ti3C2Tx MXene composites. | |
Electrochemical performance of MoS2/Ti3C2Tx composites for ZIBs
Zn//MoS2/Ti3C2Tx MXene batteries were constructed utilizing MoS2/Ti3C2Tx MXene as cathode and zinc as anode with electrolyte consisted of 21 mol L−1 LiTFSI and 1 mol L−1 Zn(CF3SO3)2, respectively (Fig. 3a). The electrochemical performance of MoS2/Ti3C2Tx MXene composites was investigated through GCD and rate capability of Zn//MoS2/Ti3C2Tx MXene batteries between 0 V and 1.6 V as demonstrated in Fig. 3b and c. Zn//MoS2/Ti3C2Tx batteries displayed specific discharge capacities of 277.8, 228.5, 175.6, 138.9 and 106.4 mA h g−1 at current densities of 0.1, 0.2, 0.5, 1.0, and 2.0 A g−1, respectively. The specific discharge capacities were found to be higher than that of MoS2 (Fig. 3c and S8†), MoS2 with 1 mol L−1 Zn(CF3SO3)2 electrolyte (Fig. S9†) and other MoS2-based ZIBs as presented in Fig. 3d and Table S1.†31–35,37,45–53 This was mainly attributed to the increased specific surface area of MoS2/Ti3C2Tx MXene composites in Fig. S10.† When the current density returned to 0.1 A g−1, the corresponding discharge capacity recovered to approximately 233.0 mA h g−1 maintaining about 84% of the original discharge capacity. This indicated the good electrochemical reversibility and fast reaction kinetics of the prepared ZIBs. Furthermore, the prepared ZIBs using MoS2/Ti3C2Tx MXene composites exhibited a power density of 37.7 W kg−1 and an energy density of 108.3 W h kg−1. Ascribing to the introduction of Ti3C2Tx MXene, the vertically aligned heterostructure with expanded interlayer spacing and good electrolyte-philic properties (Fig. S11†) of MoS2 generated the considerable electrochemical properties.
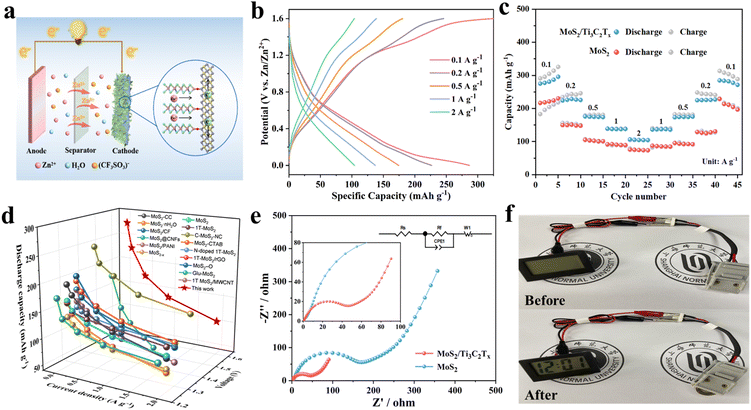 |
| Fig. 3 Electrochemical performances of Zn//MoS2/Ti3C2Tx MXene batteries in 21 mol L−1 LiTFSI and 1 mol L−1 Zn(CF3SO3)2 aqueous electrolyte. (a) Schematics of the mechanism of Zn//MoS2/Ti3C2Tx MXene battery. (b) The galvanotactic charge/discharge curves and (c) rate capability of Zn//MoS2/Ti3C2Tx MXene batteries under various current densities. (d) Discharge capacity of ZIBs compared with the values reported of other MoS2 based ZIBs. (e) Electrochemical impedance spectroscopy spectra of Zn//MoS2/Ti3C2Tx and Zn//MoS2 batteries. Inset: the partial enlargement EIS at the high frequency region. (f) Digital photographs of Zn//MoS2/Ti3C2Tx MXene batteries to power a lock. | |
From the EIS spectra in Fig. 3e, Nyquist diagram possessed a semicircle in the high-frequency region and a diagonal line in the low-frequency region. The intercept on the real axis and diameter of the semicircle reflected the equivalent series resistance (Re) and the charge-transfer resistance (Rct), respectively.54 The slope of diagonal line in the low-frequency region indicates Warburg resistance (Zw) caused by ion diffusion in the electrode. The Zn//MoS2/Ti3C2Tx batteries displayed smaller Rct (31.1 Ω) than that of Zn//MoS2 batteries (114.7 Ω), attributed to the high conductivity and reduced the zinc ions intercalation energy barrier of the 2D/2D MoS2/Ti3C2Tx heterostructure. Furthermore, MoS2/Ti3C2Tx composites exhibited decreased Zw compared to MoS2 and commercial MoS2, signifying the faster diffusion rate of Zn2+ and improved ion conductivity with introduction of conductive Ti3C2Tx in Fig. S12.† Remarkably, an exceptionally long lifetime of 5000 cycles was obtained with stable capacity retention of over 80% when cycled at high current density of 10.0 A g−1 (Fig. S13†), better than that of Zn//MoS2 batteries using 1 mol L−1 Zn(CF3SO3)2 electrolyte (Fig. S14†). The MoS2/Ti3C2Tx MXene heterostructure structure with expanded layer spacing was conducive to intercalation/delamination of zinc ion. The morphologies of MoS2/Ti3C2Tx MXene nanosheets were well preserved without amount of aggregation after cycling measurements (Fig. S15†). Furthermore, the interlayer spacing of MoS2/Ti3C2Tx MXene composites well maintained with obvious lattice fringes after long-term cycle test (Fig. S16†). Moreover, at low current density of 1.0 A g−1, capacity can be maintained about 80% of initial capacity after 800 charge/discharge cycles (Fig. S17†), indicating excellent structural stability for ZIB. In order to explore the practical application value of ZIBs, one Zn//MoS2/Ti3C2Tx MXene ZIB can illuminate a clock (Fig. 3f), revealing that the prepared ZIBs can be used as electrochemical storage device to applied other electronic products.
Kinetics of Zn//MoS2/Ti3C2Tx ZIBs
The CV curve was obtained at different sweep rates within the voltage window of 0–1.6 V vs. Zn/Zn2+ in Fig. 4a. With the increase of scanning rate from 0.4 mV s−1 to 1.2 mV s−1, the area of the CV curve gradually increased along with obviously enhancement in current intensity of the redox peak. This was because the diffusion resistance increased with the increase of sweep rate. At scanning rate of 0.1 mV s−1, the couple cathode peak and anode peak severally represented at 0.27 V and 1.25 V, in accordance with the discharge and charge plateaus in GCD curves (Fig. 3b), corresponding to insertion/desertion of zinc ions. Based on the CV curves obtained at various rates, electrochemical kinetic processes of Zn//MoS2/Ti3C2Tx batteries can be determined by the following relation:
where a and b were variable parameters, i and v represented peak current and the corresponding scan rate, respectively. In general, while the co-efficient b value equaled to 1 or 0.5, the electrochemical process was dominated by capacitive-limited controlled behavior or diffusion-limited processes, respectively. From the slope fitting curves in Fig. 4b, the b values of peaks 1 and 2 were separately calculated as 0.80 and 0.88, revealing that capacitive-limited process and diffusion-controlled behavior synergistically dominated the charge storage process of MoS2/Ti3C2Tx composites. Moreover, the capacitive (k1ν) contribution and diffusion (k2ν1/2) contribution of MoS2/Ti3C2Tx composites can be further rationally quantified by the following equation:
where k1 and k2 were parameters changed with the peak current (i). Fig. 4c illustrated the ratio of the capacitive contribution (blue) to the diffusion contribution (red) as a function of scan rate. The value of capacitive contribution exhibited nearly 65.2% at the scan rate of 0.4 mV s−1 (Fig. 4d). This value steadily increased with increasing scan rates due to the slower lower capacitive-limited process compared to diffusion-controlled behavior.
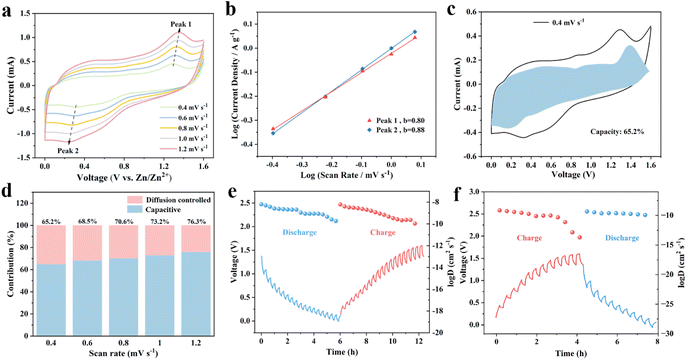 |
| Fig. 4 (a) Cyclic voltammogram profiles of Zn//MoS2/Ti3C2Tx batteries at various scan rates. (b) The fitting plots between log(i) and log(v) at various peak currents. (c) Quantification of the capacitive (blue area) and diffusion charge storage in the MoS2/Ti3C2Tx electrode at a scan rate of 0.4 mV s−1 and (d) the ratio of the capacitive contribution (blue) to the diffusion contribution (red) as a function of scan rate. Charge/discharge GITT curves and corresponding Zn2+ diffusion coefficients for (e) MoS2/Ti3C2Tx and (f) MoS2 at 0.5 A g−1. | |
The kinetics of Zn2+ intercalation during the charge/discharge reaction of MoS2/Ti3C2Tx cathode material was studied in depth using the GITT. The diffusion coefficient of Zn2+
was calculated using the following equation:
where the variables
τ,
M,
m,
Vm and
A severally represented the relaxation time, molar mass of active material, mass of active material, molar volume, and the contact area between electrode and electrolyte. Additionally, Δ
Es and Δ
Eτ represented the pulse voltage change and voltage change of constant-current charge/discharge, respectively. In the voltage range of 0–1.6 V, the

of MoS
2/Ti
3C
2T
x MXene ZIBs were calculated to be in the range of 10
−8 to 10
−10 cm
2 s
−1 (
Fig. 4e), which was superior to that of MoS
2 (10
−9 to 10
−14 cm
2 s
−1,
Fig. 4f), and other previously reported modified-MoS
2 electrode materials (10
−10 to 10
−14 cm
2 s
−1).
32,45 The improved performance of the Zn//MoS
2/Ti
3C
2T
x MXene ZIBs can be attributed to the introduction of Ti
3C
2T
x into MoS
2, which increased the contact area, shortened the transport distance of Zn
2+ and generated the accelerated migration rate of Zn
2+. The increase of charge transfer rate and the rapid diffusion of Zn
2+ ensured the excellent rate performance and cycle stability of the Zn//MoS
2/Ti
3C
2T
x MXene ZIBs.
Mechanism of Zn//MoS2/Ti3C2Tx ZIBs
Ex situ XRD characterization and XPS measurements were performed to investigate the Zn storage mechanism of MoS2/Ti3C2Tx electrode. Specifically, the charge–discharge marked states (points A–G) were selected for ex situ XRD testing (Fig. 5a), focusing on the structural evolution of MoS2/Ti3C2Tx electrode. During the discharge process (A–D), the (002) characteristic peak of MoS2/Ti3C2Tx electrode shifted to the lower angle, demonstrating that the insertion of Zn2+ ions with expanding the layer spacing of MoS2/Ti3C2Tx electrode. After charging (D–G), the (002) peak position returned to the original point A, which was caused by the desertion of Zn2+ ions from the MoS2/Ti3C2Tx electrode. The charge/discharge process was consistent with the CV curves (Fig. 4a). The results indicated that the structure of MoS2/Ti3C2Tx possessed good reversibility without collapsing during the ion embedding-detachment process.
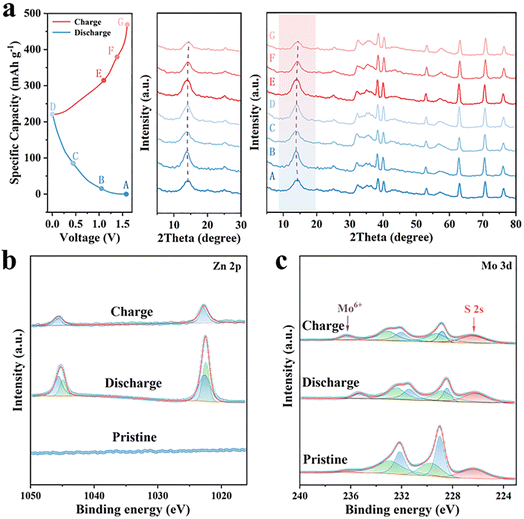 |
| Fig. 5 Zn-storage mechanism of MoS2/Ti3C2Tx composites. (a) Charge/discharge profiles of Zn//MoS2/Ti3C2Tx battery at a current density of 0.1 A g−1. The ex situ XRD patterns collected at different charge/discharge depths. The ex situ high-resolution XPS spectroscopy of (b) Zn 2p and (c) Mo 3d at different charge/discharge depths. | |
The reversible insertion/extraction mechanism of Zn2+ was also confirmed through XPS measurements (Fig. 5b and c). As expected, no diffraction signal of Zn 2p was detected in the pristine condition. Nevertheless, two remarkable diffraction peaks were observed at 1045.8 eV and 1022.7 eV while discharged, corresponding to Zn 2p1/2 and Zn 2p3/2. The diffraction peak indicated the insertion of Zn2+ to the MoS2/Ti3C2Tx electrode and the adsorption of Zn2+ in the electrolyte due to the capacitive behavior in consistent with the b value in CV measurement (Fig. 4d). Upon reverse charging, the inserted portion of Zn2+ disappeared from the diffraction peak but the adsorbent portion remained, indicating the reversible insertion/extraction of Zn2+. The effect of Zn2+ on the valence changes of Mo elements can be evidenced in the ex situ XPS patterns (Fig. 5c). With the insertion of Zn2+ at discharged state, the S 2s peak shifted by about 0.2 V to the lower binding energy and the intensity of Mo6+ was aggressively enhanced. Conversely, the S 2s peak returned to its original state and the intensity of Mo6+ significantly decreased at the discharged state. These results confirmed the zinc storage mechanism of MoS2/Ti3C2Tx electrode which agreed well with the ex situ XRD results (Fig. 5a).
As mentioned above, it can be calculated that 0.83 Zn2+ can be inserted into per molecule of MoS2 at the current density of 0.1 A g−1. Consequently, the electrochemical mechanism of the MoS2/Ti3C2Tx battery can be illustrated and formulated as following:
Cathode: 0.83Zn2+ + 1.66e− + MoS2 ↔ Zn0.83MoS2 |
During the discharged process, Zn anode lost the electron to be reduced to Zn2+. Simultaneously, Zn2+ ions were intercalated into the MoS2 to establish the phase of Zn0.83MoS2 at the cathode. During the reverse charging, Zn2+ ions were gradually extracted from Zn0.83MoS2 to re-established the MoS2 phase, while the Zn2+ gained the electron to deposit on the anode.
Conclusions
In summary, MoS2 nanosheets were successfully vertically grown on monodisperse MXene composites through a one-step hydrothermal method. The electronical conductivity and hydrophilicity in electrolyte of the composite were effectively improved compared with unmodified MoS2. Meanwhile, the self-aggregation of MoS2 and volume expansion during the charge/discharge reaction were significantly suppressed, resulting in excellent electrochemical properties with fast reaction kinetics. As a result, the MoS2/Ti3C2Tx cathode demonstrated discharge specific capacity of up to 277.8 mA h g−1 at 0.1 A g−1 and the capacity retention of 80% after 5000 cycles when the current density was 10.0 A g−1. This work provided more possibilities for improving the electrochemical performance of energy storage layered materials.
Author contributions
W. Su contributed to most experimental work. M. Lang completed the required experiments in the revised manuscript. Q. Zhang and Y. Yang assisted in characterization of some materials. H. Li conceived this idea and wrote the manuscript. F. Zhang conceived this idea and supervised the work. All the authors assisted in experiments and provided constructive comments on the text.
Conflicts of interest
There are no conflicts of interest.
Acknowledgements
This work is supported by The National Natural Science Foundation of China (22076122 and 52203269), The Shanghai Sailing Program (No. 20YF1435100), and Shanghai Government (22ZR1480200, 19SG42).
References
- X. Jia, C. Liu, Z. G. Neale, J. Yang and G. Cao, Chem. Rev., 2020, 120, 7795–7866 CrossRef CAS PubMed.
- W. S. V. Lee, T. Xiong, X. Wang and J. Xue, Small Methods, 2021, 5, 2000815 CrossRef CAS PubMed.
- L. Cao, D. Li, T. Deng, Q. Li and C. Wang, Angew. Chem., Int. Ed., 2020, 132, 19454–19458 CrossRef.
- Y. Li, Z. Wang, Y. Cai, M. Pam, Y. Yang, D. Zhang, Y. Wang and S. Huang, Energy Environ. Mater., 2022, 5, 823–851 CrossRef CAS.
- T. Wang, C. Li, X. Xie, B. Lu, Z. He, S. Liang and J. Zhou, ACS Nano, 2020, 14, 16321–16347 CrossRef CAS PubMed.
- D. Kundu, B. D. Adams, V. Duffort, S. H. Vajargah and L. F. Nazar, Nat. Energy, 2016, 1, 1–8 Search PubMed.
- H. Li, L. Ma, C. Han, Z. Wang, Z. Liu, Z. Tang and C. Zhi, Nano Energy, 2019, 62, 550–587 CrossRef CAS.
- A. Kanwade, S. Gupta, A. Kankane, M. K. Tiwari, A. Srivastava, J. A. K. Satrughna, S. C. Yadav and P. M. Shirage, RSC Adv., 2022, 12, 23284–23310 RSC.
- S. Luo, L. Xie, F. Han, W. Wei, Y. Huang, H. Zhang, M. Zhu, O. G. Schmidt and L. Wang, Adv. Funct. Mater., 2019, 29, 1901336 CrossRef.
- Z. Yuan, L. Wang, D. Li, J. Cao and W. Han, ACS Nano, 2021, 15, 7439–7450 CrossRef CAS PubMed.
- N. Zhang, X. Chen, M. Yu, Z. Niu, F. Cheng and J. Chen, Chem. Soc. Rev., 2020, 49, 4203–4219 RSC.
- N. Guo, W. Huo, X. Dong, Z. Sun, Y. Lu, X. Wu, L. Dai, L. Wang, H. Lin, H. Liu, H. Liang, Z. He and Q. Zhang, Small Methods, 2022, 6, 2200597 CrossRef CAS PubMed.
- Y. Shi, Y. Chen, L. Shi, K. Wang, B. Wang, L. Li, Y. Ma, Y. Li, Z. Sun and W. Ali, Small, 2020, 16, 2000730 CrossRef CAS PubMed.
- S. Li, S. Zhang, T. Feng, H. Zhou and M. Wu, RSC Adv., 2022, 12, 18466–18474 RSC.
- S. Li, Y. Liu, X. Zhao, K. Cui, Q. Shen, P. Li, X. Qu and L. Jiao, Angew. Chem., Int. Ed., 2021, 60, 20286–20293 CrossRef CAS PubMed.
- M. Wu, G. Zhang, H. Yang, X. Liu, M. Dubois, M. A. Gauthier and S. Sun, InfoMat, 2022, 4, e12265 CAS.
- N. Subjalearndee, N. He, H. Cheng, P. Tesatchabut, P. Eiamlamai, P. Limthongkul, V. Intasanta, W. Gao and X. Zhang, Adv. Fiber Mater., 2022, 4, 457–474 CrossRef CAS.
- J. Xu, Y. Liu, P. Chen, A. Wang, K.-j. Huang, L. Fang and X. Wu, J. Colloid Interface Sci., 2022, 620, 119–126 CrossRef CAS PubMed.
- J. Xu, S. Zhang, Z. Wei, W. Yan, X. Wei and K. Huang, J. Colloid Interface Sci., 2021, 585, 12–19 CrossRef CAS PubMed.
- F. Zhang, M. Du, Z. Miao, H. Li, W. Dong, Y. Sang, H. Jiang, W. Li, H. Liu and S. Wang, InfoMat, 2022, 4, e12346 CAS.
- L. Wang, X. Tan, Q. Zhu, Z. Dong, X. Wu, K. Huang and J. Xu, J. Power Sources, 2022, 518, 230747 CrossRef CAS.
- H. Jia, K. Liu, Y. Lam, B. Tawiah, J. H. Xin, W. Nie and S.-X. Jiang, Adv. Fiber Mater., 2023, 5, 36–58 CrossRef CAS.
- J. Song, K. Xu, N. Liu, D. Reed and X. Li, Mater. Today, 2021, 45, 191–212 CrossRef CAS.
- L. Ma, M. A. Schroeder, O. Borodin, T. P. Pollard, M. S. Ding, C. Wang and K. Xu, Nat. Energy, 2020, 5, 743–749 CrossRef CAS.
- X. Yao, C. Li, R. Xiao, J. Li, H. Yang, J. Deng and M. S. Balogun, Small, 2022, 18, 2204534 CrossRef CAS PubMed.
- X. Wu, X. Xie, H. Zhang and K.-J. Huang, J. Colloid Interface Sci., 2021, 595, 43–50 CrossRef CAS PubMed.
- J. Xu, Q. Liu, Z. Dong, L. Wang, X. Xie, Y. Jiang, Z. Wei, Y. Gao, Y. Zhang and K. Huang, ACS Appl. Mater. Interfaces, 2021, 13, 54974–54980 CrossRef CAS PubMed.
- X. Geng, Y. Jiao, Y. Han, A. Mukhopadhyay, L. Yang and H. Zhu, Adv. Funct. Mater., 2017, 27, 1702998 CrossRef.
- H. Sun, H. Liu, Z. Hou, R. Zhou, X. Liu and J.-G. Wang, Chem. Eng. J., 2020, 387, 124204 CrossRef.
- J. Xu, Z. Dong, K. Huang, L. Wang, Z. Wei, L. Yu and X. Wu, Scr. Mater., 2022, 209, 114368 CrossRef CAS.
- M. Huang, Y. Mai, G. Fan, X. Liang, Z. Fang and X. Jie, J. Alloys Compd., 2021, 871, 159541 CrossRef CAS.
- H. Liu, J.-G. Wang, W. Hua, Z. You, Z. Hou, J. Yang, C. Wei and F. Kang, Energy Storage Mater., 2021, 35, 731–738 CrossRef.
- J. Liu, N. Gong, W. Peng, Y. Li, F. Zhang and X. Fan, Chem. Eng. J., 2022, 428, 130981 CrossRef CAS.
- C. Li, C. Liu, Y. Wang, Y. Lu, L. Zhu and T. Sun, Energy Storage Mater., 2022, 49, 144–152 CrossRef.
- W. Xu, C. Sun, K. Zhao, X. Cheng, S. Rawal, Y. Xu and Y. Wang, Energy Storage Mater., 2019, 16, 527–534 CrossRef.
- S. Li, Y. Liu, X. Zhao, K. Cui, Q. Shen, P. Li, X. Qu and L. Jiao, Angew. Chem., Int. Ed., 2021, 133, 20448–20455 CrossRef.
- M. Huang, Y. Mai, L. Zhao, X. Liang, Z. Fang and X. Jie, Electrochim. Acta, 2021, 388, 138624 CrossRef CAS.
- Y. Dong, H. Shi and Z. S. Wu, Adv. Funct. Mater., 2020, 30, 2000706 CrossRef CAS.
- R. Zhao, A. Elzatahry, D. Chao and D. Zhao, Matter, 2022, 5, 8–10 CrossRef CAS.
- X. Tang, X. Guo, W. Wu and G. Wang, Adv. Energy Mater., 2018, 8, 1801897 CrossRef.
- F. Ming, H. Liang, G. Huang, Z. Bayhan and H. N. Alshareef, Adv. Mater., 2021, 33, 2004039 CrossRef CAS PubMed.
- Y. An, Y. Tian, J. Feng and Y. Qian, Mater. Today, 2022, 52, 146–179 CrossRef.
- Q. Zhang, H. Lai, R. Fan, P. Ji, X. Fu and H. Li, ACS Nano, 2021, 15, 5249–5262 CrossRef CAS PubMed.
- S. Li, Y. Liu, X. Zhao, Q. Shen, W. Zhao, Q. Tan, N. Zhang, P. Li, L. Jiao and X. Qu, Adv. Mater., 2021, 33, 2007480 CrossRef CAS PubMed.
- M. Huang, Y. Mai, L. Zhao, X. Liang, Z. Fang and X. Jie, ChemElectroChem, 2020, 7, 4218–4223 CrossRef CAS.
- J. Liu, P. Xu, J. Liang, H. Liu, W. Peng, Y. Li, F. Zhang and X. Fan, Chem. Eng. J., 2020, 389, 124405 CrossRef CAS.
- Z. Zhang, W. Li, R. Wang, H. Li, J. Yan, Q. Jin, P. Feng, K. Wang and K. Jiang, J. Alloys Compd., 2021, 872, 159599 CrossRef CAS.
- Y.-T. Wang, Z.-Z. Zhang and M.-X. Li, Nano Futures, 2022, 6, 025001 CrossRef.
- L. Liu, W. Yang, H. Chen, X. Chen, K. Zhang, Q. Zeng, S. Lei, J. Huang, S. Li and S. Peng, Electrochim. Acta, 2022, 410, 140016 CrossRef CAS.
- P. Cao, N. Chen, W. Tang, Y. Liu, Y. Xia, Z. Wu, F. Li, Y. Liu and A. Sun, J. Alloy and Compd., 2022, 898, 162854 CrossRef CAS.
- Z. Sheng, P. Qi, Y. Lu, G. Liu, M. Chen, X. Gan, Y. Qin, K. Hao and Y. Tang, ACS Appl. Mater. Interfaces, 2021, 13, 34495–34506 CrossRef CAS PubMed.
- Y. Q. Jin, H. Chen, L. Peng, Z. Chen, L. Cheng, J. Song, H. Zhang, J. Chen, F. Xie, Y. Jin, J. Shi and H. Meng, Chem. Eng. J., 2021, 416, 127704 CrossRef CAS.
- H. Jia, M. Qiu, B. Tawiah, H. Liu and S. Fu, Compos. Commun., 2021, 27, 100841 CrossRef.
- Z. Yao, W. Zhang, X. Ren, Y. Yin, Y. Zhao, Z. Ren, Y. Sun, Q. Lei, J. Wang, L. Wang, T. Ji, P. Huai, W. Wen, X. Li, D. Zhu and R. Tai, ACS Nano, 2022, 16, 12095–12106 CrossRef CAS PubMed.
|
This journal is © The Royal Society of Chemistry 2023 |
Click here to see how this site uses Cookies. View our privacy policy here.